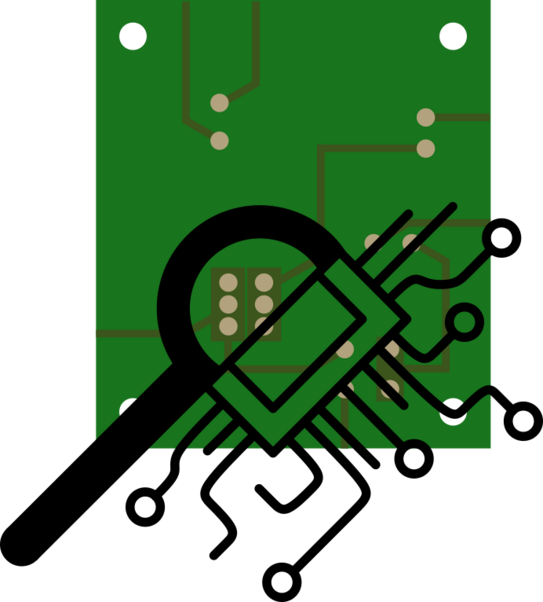
AQR 4.0
Autonomous quality control using machine learning methods (Project processing ist carried out by RIF e.V., Production Systems Department)
Problem
Maintaining a consistently high product quality and achieving this product quality in the shortest possible process time are two key challenges in the production of surface-mounted devices (SMD). They describe the goal of harmonising quality and production speed in such a way that economical production is possible without compromising the reliability of the products.
Objective
The core of the project is the development of an autonomous quality control system using machine learning methods in order to significantly reduce inspection and quality costs in the production plant through robust and efficient processes. To achieve this goal, information technology, statistics and domain knowledge are combined. The focus here is on proven approaches from Six Sigma, machine learning and modern data processing.
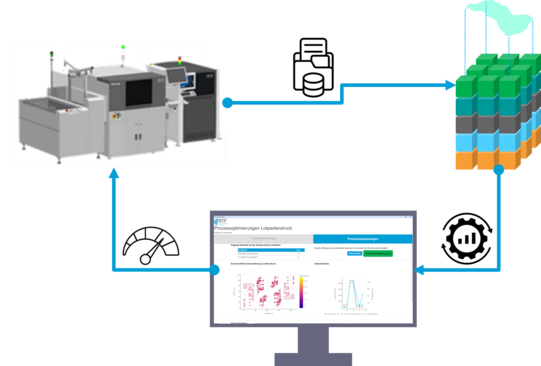
Approach
The key components of the developed method are:
- Data from the solder paste inspection (LIS, SPI for short) is used for continuous monitoring and optimisation of the solder paste pressure.
- Continuous process adjustment to ensure product quality is carried out by means of automatically suggested setting parameters using a specially developed, adapted self-organising map (SOM).
- The developed SOM enables the simultaneous evaluation of several process parameters - both in terms of quality and process time - in order to find the ideal compromise between efficiency and reliability.
These intelligent adjustments significantly reduce production time on the one hand and waste on the other. This method was filed with the European Patent Office on 18 April 2024 under application number EP24171067.2 and with the title ‘Method for setting up a production device and production system’ and will be published on 18 October 2025.