AutoEdge
Automation of the Beam Cutting Process for the Preparation of Tool Cutting Edges
Problem
Optimising individual processes in the manufacture of cutting tools can increase their performance and thus strengthen the economic position of tool manufacturers. In this context, the use of preparation processes for the treatment of solid carbide tools before coating, during tool manufacture and, in particular, the targeted adaptation of the cutting edge shape to the machining task at hand are becoming increasingly important. The advantages here are that an increase in edge stability leads to significantly improved wear resistance of the cutting edges. In addition, the quality of the coating can be improved by introducing residual compressive stresses and smoothing the surface of the coating.
However, due to the lack of flexibility of the preparation processes available industrially to date, the preparation of uncoated tools of low complexity, which is already used industrially, is largely carried out with standardised cutting edge roundings and without specific adaptation to the tool and the application. In order to be able to use the technological and economic potential of the preparation of cutting tools, it must be ensured that an economic application of the preparation processes is possible on the basis of an efficient process design along the entire manufacturing chain. However, systems for the targeted local preparation of tools are currently only available at a few research institutions. Their programming and in particular the generation of the necessary movement paths of the handling devices are currently still very complex and are therefore usually carried out manually. For this reason, these systems are only suitable for industrial use to a limited extent. The trend towards ever-smaller batch sizes, with an increasing variety of variants, right up to cutting tools specially made for a particular application, places great demands on the system technology and especially on its programming. However, flexible and changeable use of production systems and, in particular, their fast and efficient retooling are decisive for the economic efficiency of the process of targeted preparation of cutting tools.
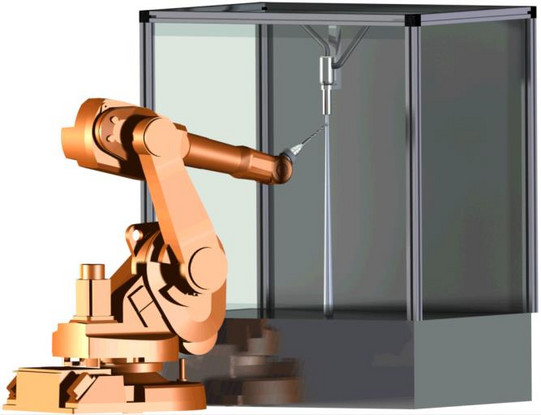
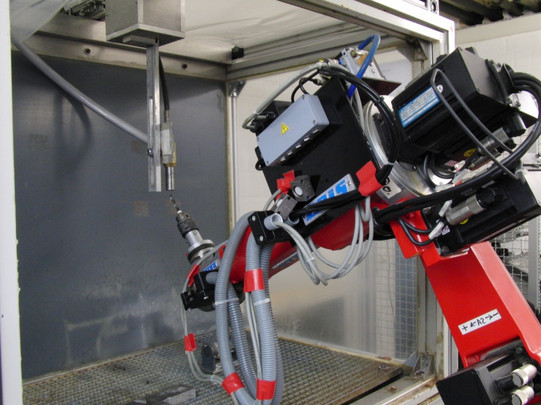
Objective
The aim of this project is to establish a targeted cutting edge preparation on cutting tools by means of the robot-assisted wet-jet chip removal process with abrasive medium using an automated approach for path generation. This should enable the flexible cutting process-specific adjustment of the cutting edge shape of complex cutting tools to the cutting process and the integration of this preparation process into the industrial production chain.
Procedure
In order to achieve this goal, the following approach is being pursued within the framework of the project: On the one hand, a process data basis is to be generated that enables a tool-specific targeted preparation of cutting tools. The application spectrum covers a selection of typical cutting tools, including drills, but should also be able to be designed for other tool types such as milling and threading tools. This should ensure a function-oriented micro-design of all cutting tool types with a geometrically defined cutting edge. On the other hand, the process of wet-jet machining must be economically applicable in the production of cutting tools. Therefore, another main task of the project is to develop a suitable system configuration including a methodology for CAD data-based system programming, using automated path generation based on determined process influencing variables.
Research- and Development Partner
ISF, TU Dortmund
carat robotic innovation GmbH
Funding Reference
The AutoEdge ZIM project is funded by the Federal Ministry of Economics and Technology via the AiF as part of the Central Innovation Programme for Medium-sized Enterprises on the basis of a resolution of the German Bundestag.