CSC - Cyber System Connector
Intelligently create and use machine documentation
(Project duration November 2013 to October 2016)
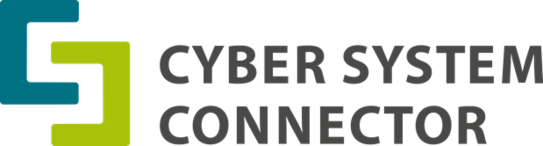
Problem
When handing over and commissioning plants, the manufacturer is obliged under the Machinery Directive to include documentation that conforms to the standards. The requirements for this technical documentation are constantly increasing with the growing complexity of machines and systems, in particular due to the increasing integration of a multitude of electronic control elements and decentrally organised computer units. Due to the resulting high time and cost expenditure of the technical documentation, the status of the documents is hardly kept up to date after delivery and start-up of the systems. In the case of technical conversions or upgrades due to product changes, optimisation measures or production volume adjustments, for example, the resulting changes are usually only added to the documentation or not entered at all. Especially for future factories with decentralised self-organisation of production, adapted documentation and maintenance processes are required. New strategies for these tasks must be developed and implemented, especially to manage the increasing complexity and networking of production facilities.
Objective
The aim of the CSC research project is to ensure up-to-date technical documentation by means of a virtual image of the systems throughout the entire product creation process. The CyberSystemConnector (CSC) forms the interface for each integrated system component of a machine and plant. Every change to the system, and thus to the technical documentation, is fed back into a virtual image of the system. This means that there is always a virtual image of the plant that is equivalent to the real plant. The system automatically checks whether the existing safety concepts of the machines and systems can still be complied with after the changes or whether there is a need for action.
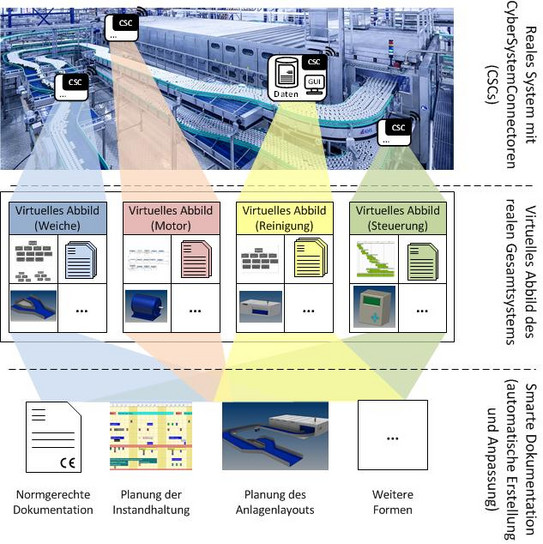
By using CSC, the enormous effort of technical documentation for today's plants can be reduced. Maintenance processes can be efficiently planned and carried out using the virtual image. The project result is validated through prototypical implementation at user companies in the mechanical and plant engineering sector. The users from the different industries thereby ensure a development that is not an industry-specific or niche solution, but has a broad impact in German mechanical and plant engineering.
Procedure
Based on an analysis of existing maintenance and documentation strategies of the users (KHS, Cloos, IBG, Esser und Partner) as well as the current state of the art, requirements for corresponding processes in cyber-physical systems are specified. In cooperation with the users and the IPS, a process for the dynamic, decentralised processing of documentation and machine data is being developed by the software developers Cognitas and PDTec. With the help of the CSC to be developed by the IPS, the communication of all plant components and change tracking will be implemented. The validation of the function of the CSCs and in particular the self-organised acquisition of the digital image of the plant as well as the compliance with the timeliness is carried out in the demonstrators of the research institution IPS and at the users of the consortium.
Research- and Development Partner
- KHS GmbH
- cognitas Society for Technical Documentation mbH
- PDTec AG
- Carl Cloos Welding Technology GmbH
- IBG Automation GmbH
Funding Reference
This research and development project is funded by the Federal Ministry of Education and Research under the framework concept "Research for the Production of Tomorrow" and is supervised by the project management organisation Projektträger Karlsruhe. The responsibility for the content of this publication lies with the author.