InnoLern
Participative improvement of the innovation and learning culture of companies in regional networks (InnoLern)
Problem
The ability of small and medium-sized enterprises (KMU) to quickly adapt business processes to global market requirements is an important prerequisite for the stability and future prospects of companies in the region. For this, companies need creative employees and innovation-friendly organisational structures that create the conditions to sustainably strengthen the adaptability of companies. Creating these innovation-friendly structures and empowering employees to engage creatively in improving processes (participatory approach) are not at the forefront of day-to-day business for most KMUs.
To strengthen the competitiveness of companies through creative and innovative employees in the region, 13 companies from the network Industrie RuhrOst e. V. are working together with staff from ForTrans e. V. and the Chair of Work and Production Systems at TU Dortmund University.
Objective
The goals of the InnoLern project can be differentiated company-related and network-related. On the company-related level, operative employees of the participating companies are trained in modern methods of industrial engineering and project management according to their needs. At the network level, the operative employees are systematically networked and the knowledge transfer between the companies is stimulated. The establishment of a cross-company culture of trust is central. The culture of trust lays the foundation for an open and honest discussion with employees from other companies about the challenges of one's own company. This network-based exchange supports the finding of new, innovative solutions for continuous and sustainable improvement in the organisation of production. The exchange also enables employees to learn new ideas and techniques and to bring them into their own company. Central aspects in the InnoLern project are:
- To increase the adaptability and modernisation capacity of companies through organisational measures,
- to train the creativity of employees and to use it in a targeted way,
- to exchange ideas and techniques across companies,
- to improve the organisation of production and
- to further develop leadership skills.
Procedure
In the first phase, so-called modernisation coaches are trained in each company. Modernisation coaches are operational staff and have the task of initiating and promoting process improvements in the companies in the future. Each company starts with a concrete pilot project. The foundations for such an approach to improving company processes are laid in a training course. The training imparts current methods and techniques of industrial engineering and teaches the methods of project management (see Figure 1).
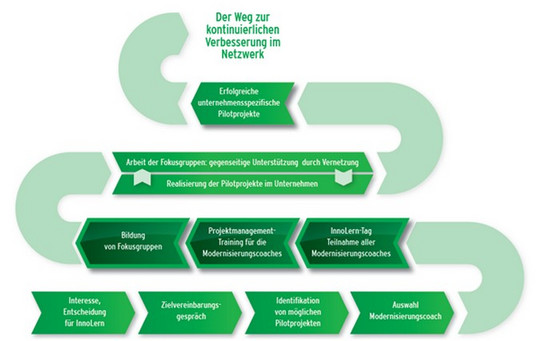
The professional exchange of new ideas and techniques takes place in small groups (focus groups). During a focus group meeting, all participating modernisation coaches start by presenting their current project progress in their own pilot project before the project progress of the inviting modernisation coach is discussed in detail and in a professionally sound manner (collegial consultation).
ForTrans e. V. and the Chair of Work and Production Systems moderate the exchange process between the modernisation coaches and support the successful realisation of the pilot projects. Further training courses are offered according to need.
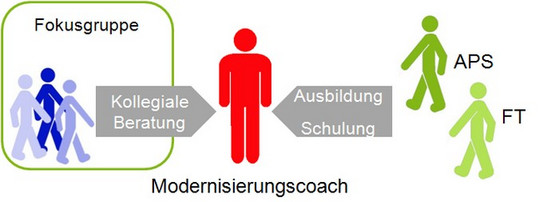
Research- and Development Partner
ForTrans e.V., organisational psychology, social and leadership skills training, www.fortrans.de
Netzwerk Industrie Ruhr-Ost (NIRO), Contact: Pascal Lampe (Managing Director)
Numerous companies from Netzwerk Industrie RuhrOst e. V.
Funding Reference
The project funding is provided by the State of NRW. This grant includes funds from the European Union - European Social Fund (ESF).