VEIN
Trust and Learning in the Incremental, Error-Induced Innovation Process
(Project duration: August 2009 to April 2013)
Problem
In pursuit of advantages in international competition, many companies rely on continuous improvement processes (CIP) as a crucial success factor. Programmes to initiate such a process are closely linked to the adaptation of the Toyota Production System (TPS), with which Toyota's strong market position has been associated for many years. However, it became apparent that the mere implementation of methods and tools based on the TPS did not lead to sustainable success, as they were not geared to the specific issues in the companies. Rather, what is needed is a problem-solving-based culture of innovation that enables processes to be adapted quickly to changing customer requirements. For this, a learning and trust structure rooted in the company must be created that promotes dealing with problems in a positive sense.
Objective
Within the framework of the VEIN project, the Chair of Work and Production Systems is investigating the technical and work organisation success factors of a continuous adaptation of production processes to constantly changing customer requirements while solving the problems that arise in this context. Here, methods and tools for supporting short-cycle, continuous problem solving in a trust-based learning culture are considered experimentally among participating industrial partners.
Incremental adjustments and improvements in production processes based on the division of labour can realise innovation potentials of considerable magnitude. However, a prerequisite for this is a high level of motivation for change on the part of managers and employees. In the adaptation and improvement process coordinated by goals derived from customer requirements, this enables an innovative approach to errors. A culture of learning and trust rooted in the company must contribute significantly to this. Promoting this is therefore a core task of all management levels and, in addition to creating the technical and organisational prerequisites, is decisive for the success of sustainable, incremental process innovations. In the project, both theoretical foundations and new approaches to solutions are developed and tested experimentally. The elements and structures of a modern organisational and technical design of production processes will be identified that contribute to a high adaptability of companies in a sustainable culture of trust and error. In particular, success factors are to be identified and practicable measures for their targeted influence are to be developed and tested, which make it possible to adapt production processes to customer requirements in small steps and in short cycles. The measures to be developed should be designed in such a way that a culture of learning and trust is promoted in the company, in which a fear-free and constructive approach to problems and errors becomes a systematised and internalised part of the production system.
Procedure
The project comprises three research phases. First, success factors of incremental and short-cycle adaptation and improvement and the associated problem-solving processes are identified. In the second project phase, selected success factors will be investigated experimentally at the industrial partners. Based on the insights gained in this way, general guiding principles for action are to be derived in the final phase.
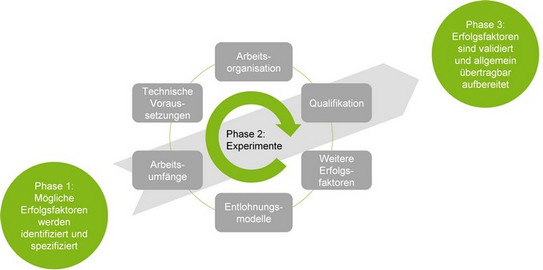
The Chair of Work and Production Systems is looking at various process-related fields of experimentation. First of all, it is to be investigated how the identification of problems in the form of deviations of the actual from the target state can be promoted. This also implies the question of how goals can be derived and communicated in a process-related manner. It is also investigated how efficient communication about problems can be ensured through technical and organisational measures and tools. A central field of experimentation is problem solving, in which methodological procedures based on the PDCA cycle will be examined more closely.
Research- and transfer partners
Chair of Information and Technology Management, Institute of Labour Science, University of Bochum
Institute for Work, Organisational and Social Psychology, Technical University of Dresden
KHS AG, Dortmund
Deutsche Edelstahlwerke GmbH, Witten
Böcker AG, Werne
Hülsmetall GmbH, Kamen
Funding Reference
This project is funded by the Federal Ministry of Education and Research and the European Social Fund of the European Union.