WaProTek
Process Architectures Conducive to Change (WaProTek)
(Project duration: July 2010 to June 2013)
Problem
Against the background of permanent technical innovations and increasingly spontaneous demand behaviour, a high capacity for change is becoming a competitive factor for manufacturing companies.
The timing and intensity of turbulent changes are hardly predictable. In response to the impulses for change, production-technical solutions have been developed up to now, the implementation of which often took several years. Therefore, a concept is needed that enables companies to react to acute change needs with a short lead time and implementation period.
In order to activate the ability to change when needed and thus be able to implement the change, practical procedures must be developed that enable the user to utilise the inherent ability to change with the least possible start-up losses.
![Wandlungsfähigkeit als Antwort auf Turbulenzen im Unternehmensumfeld [Nyhuis] Wandlungsfähigkeit als Antwort auf Turbulenzen im Unternehmensumfeld [Nyhuis]](/storages/ips-mb/_processed_/a/e/csm_WaProTek_Wandlungsf__higkeit_als_Antwort_9ee39fc8a9.jpg)
Objective
The aim of the WaProTek research project is to enable companies to identify the acute need for change in their production systems through coordinated process architectures that promote change, to identify their technical, logistical, organisational and human resources, to systematically compare them with the range of services offered by equipment suppliers and service providers, to design economic solutions and to operate them in a qualified manner. The focus here is on production systems for technologically demanding unit goods in multi-variant individual and series production.
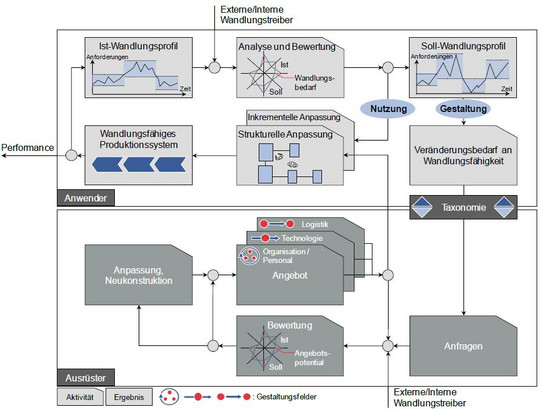
The solution approach of the WaProTek research project is based on a two-stage control loop from the point of view of the applying company, as shown below. Within the control loop, the transformation-capable production system under consideration corresponds to the controlled system and the analysis and evaluation of the system's measuring equipment. With this measuring device, a target-actual comparison of the production system's goals with the current performance and the existing transformation capabilities is carried out.
The disturbance variables affecting the system represent the so-called change drivers (e.g. legal framework conditions, raw material prices, etc.), which result in the dimensions of change. This target-performance comparison is used to assess whether the existing system flexibility is sufficient to meet the requirements (utilisation of flexibility), whether the inherent adaptability of the system can be called upon (utilisation of adaptability) or whether additional adaptability must be invested in (design of adaptability).
If it becomes apparent that the actual change profile is sufficient to control the influencing change drivers, the inherent change capability is used by the user. In doing so, the necessary adjustments are planned and implemented incrementally on a case-by-case basis within the framework of the current change profile on a technological, logistical as well as organisational and personnel level. In this way, adaptation can take place through "change in small steps" and a robust change of the production system can be ensured.
If it turns out that the inherent potential for change is not sufficient and the need for change can only be managed through structural changes, a further design control loop involving equipment suppliers is run through. This design control loop ensures a systematic comparison of the users' need for change with the available market or internal range of services.
For the communication between users and equipment suppliers in case of exceeding the threshold, a conversion-specific taxonomy of market participants is developed. This common language makes it possible to translate the need for change into concrete requests for individual solution modules and to take into account the interactions between the design fields of technology, logistics and organisation and personnel. This supports the selection and configuration of requirement-oriented and consistent solution bundles from the offerings of several equipment suppliers and different design fields to achieve the defined target transformation profile of the overall system.
The equipment suppliers process the requests and carry out an evaluation of their current offer potential, taking into account their own external and internal drivers. If an existing solution satisfies the user's requirements, it can be offered without the need for change. If the existing solutions are not sufficient, they either need to be adapted or entirely new solutions need to be developed before an offer for a transformational solution can be made. The case of a request being rejected is also conceivable.
The user uses the solution modules of different design fields from different suppliers (solution bundles) to make the structural adjustments that have been identified as necessary. By implementing these coordinated adaptable solution modules, the user is able to design the production system with the extended adaptability. The new actual change profile now corresponds to the required target change profile. New change impulses trigger the control loop again. This multi-stage control loop enables efficient design and use of the changeability.
Procedure
In addition to the control loop methodology, the most important solution components of process architectures that promote change are being developed within the framework of the project. Six competence teams of equipping and applying project partners are working on this in cooperation with the research institutes to develop and implement exemplary solutions.
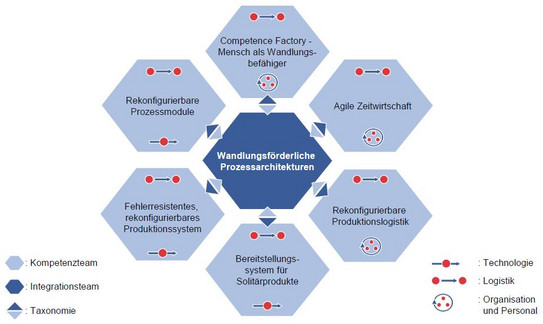
Publications
Erohin, O.; Krebs, M.; Petzelt, D.; Deuse, J.: Prospektive Planung und Gestaltung wandlungsfähiger Produktionssysteme. In: Industrie Management 27 (2011) 3, S. 45-48.
Krebs, M.; Goßmann, D.; Erohin, O.; Bertsch, S.; Deuse, J.; Nyhuis, P.: Standardisierung im wandlungsfähigen Produktionssystem. Einfluss der Prozess- und Ressourcenstandardisierung auf die Wandlungsfähigkeit. In: ZWF – Zeitschrift für wirtschaftlichen Fabrikbetrieb 106 (2011) 12, S. 912-917.
Baudzus, B.; Krebs, M.: Manuelle Montageprozesse im wandlungsfähigen Produktionssystem. In: ZWF – Zeitschrift für wirtschaftlichen Fabrikbetrieb 107 (2012) 5, S. 344-348.
Baudzus, B.; Klemke, T.: Betriebsmittel im wandlungsfähigen Produktionssystem und Strategien für deren Instandhaltung. In: Instandhaltung aktuell 77 (2012).
Research- and development partner
- Institute for Factory Installations and Logistics
- GTT Society for Technology Transfer mbH
- InSystems Automation GmbH
- LP Assembly Technology GmbH
- EWM Hightec Welding GmbH
- Mahr GmbH
- Hans Pausch GmbH & Co. KG
- Sartorius Weighing Technology GmbH (consortium leader)
- Festo Didactic GmbH & Co. KG
Further links
LINK to the project homepage: www.waprotek.de