Digital Manufacturing
In addition to the digital planning of production systems, the Digital Manufacturing research area focuses on digital operation in the Internet of Things as well as services based on this, including collaboration in value creation networks. One basis for this is the standardised modelling of production systems, which, in combination with near-real-time production data acquisition, creates the basis for the digital twin.
Meeting current Challenges
Networked IT tools are becoming increasingly important for the planning and optimisation of complex product and manufacturing structures. These support interdisciplinary work and enable the interaction of all competence carriers along the product life cycle. The Digital Manufacturing research area addresses the continuous digitalisation within the planning processes and the operation of production systems. In addition to experimental research projects, the content also includes practice-oriented digitisation projects in manufacturing companies. Future-oriented further and advanced training offers round off the portfolio of the research area.
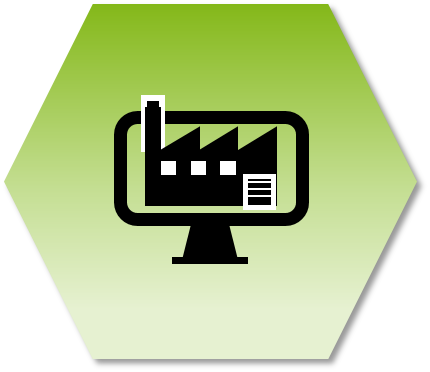
Research- and Competence Focuses
The topics of the Digital Manufacturing research area are oriented towards the cross-phase use of digital planning tools in the product engineering process (PEP) and the networking of production in the context of Industry 4.0. Thematically, it includes:
- Digital planning support in the digital factory
- Industrial Internet of Things (IIoT)
- Development and use of digital twins
- Product lifecycle management and standardisation
Methodologically, the focus is on the digital mapping of production systems and their components. This includes
- Innovative data and process modelling, including UML, SADT, EPK, PPR models, etc.
- Simulation tools, e.g. CAD, discrete-event process simulation, process planning
- Data integration, including shop-floor IT (automation pyramid), planning data or retrofitting in IIoT environments
- Data analysis and machine learning, e.g. supervised and unsupervised learning methods, anomaly detection, reference architectures
- Analysis and development of data-driven business models and services, including Canvas, Kano, X-as-a-Service.
The overarching goals are to shorten the PDP while increasing the quality of planning and the cross-divisional, value-adding use of data in production. The fields of application include
- Integrated planning processes and virtual commissioning
- AR and VR in assembly planning
- Retrofitting and use of real-time data in production through IoT technologies
- Data-driven process optimisation
- Agile product and process development
Services
Through industrial contract research, we close the gap between basic research and industrial practice. We are a competent and reliable partner for companies when it comes to questions about digitalisation in production. In doing so, we draw on a great deal of experience in industrial and scientific contexts on the one hand and on data-driven approaches on the other. Please feel free to contact us if you would like to conduct joint research with us in these areas or if we can support you in the implementation of digitalisation projects.
Current research projects in the field of Digital Manufacturing
The focus of our research is on answering quality-related questions with the help of novel, data-driven methods. As part of the validation of research results and the transfer into industrial practice, we are also continuously interested in cooperations in research projects.
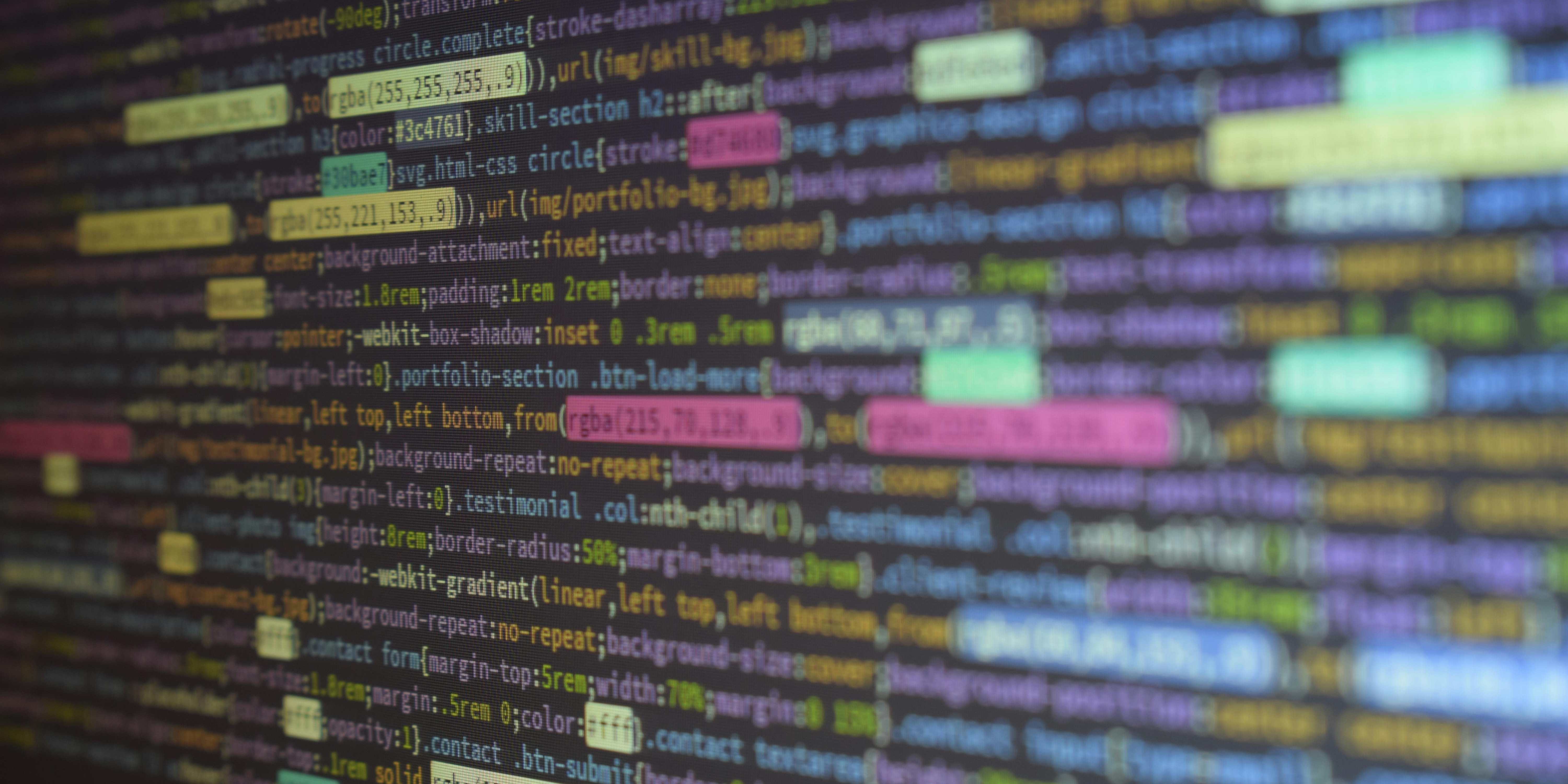
Data Science in Industrial Engineering
AI assistance system for plausibility checks, correction and creation of production plans
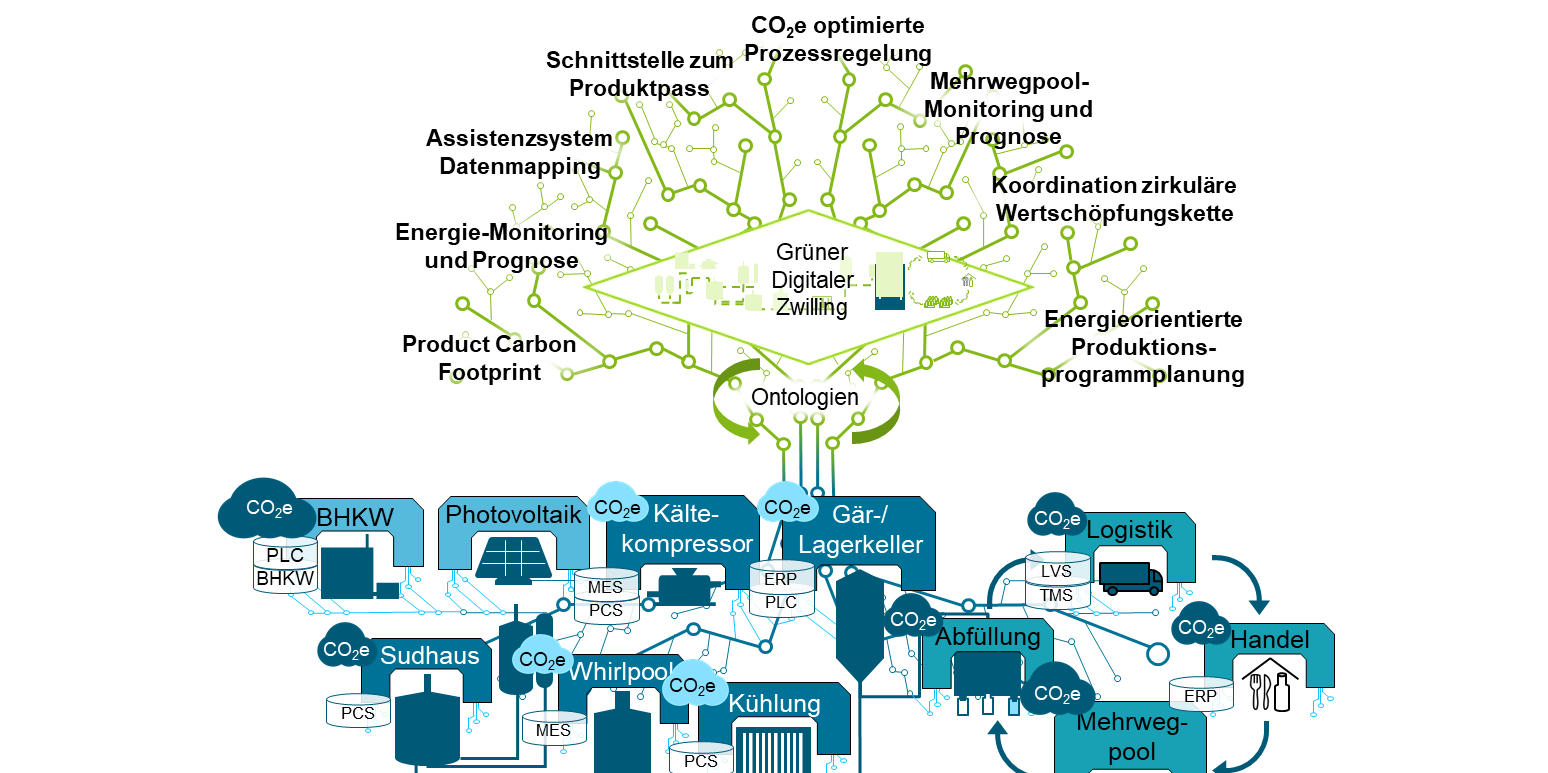
BeverGreen
Green digital twin as the basis for the sustainable transformation of the brewing and beverage industry
(Project processing ist carried out by RIF e.V., Production Systems Department)
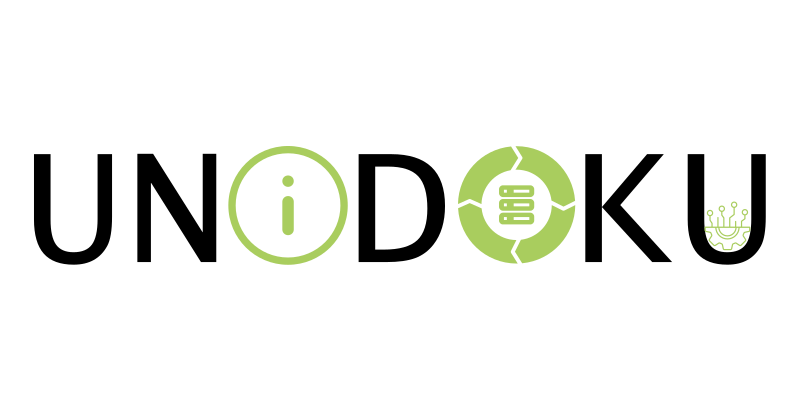
UniDoku
Universal documentation scheme for the life cycle of cyber-physical production systems