EOP
Cost-optimal Production and Stocking Strategy after End of Production (EOP)
Problem
In mechanical and plant engineering, securing post-series supply is of central importance, both on the basis of any existing obligations to make subsequent deliveries and in terms of customer loyalty. In addition, the sale of spare parts after the end of high-turnover series production (end of production) as a significant part of the after-sales service contributes to the company result. Therefore, the high potential of the after-sales business must be utilised to increase the company's profit and the post-series supply must be designed accordingly and economically.
To secure the after-sales supply, various standard strategies are used and combined into supply scenarios over the lifetime of the spare part. Here, there is the possibility of remanufacturing (internally/externally), the use of downwardly compatible parts of the series as well as the reprocessing and reuse of old parts. Each of these strategies is characterised by specific challenges, e.g. with the reuse of old parts there is the problem of an adequate return of the old parts and a correspondingly large number of returns in order to meet the given demand for spare parts.
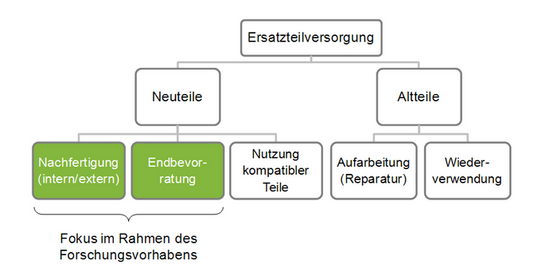
The research project described here focuses on the selection of strategies for post-series production and stockpiling of spare parts or their components. For post-series production, it is crucial to what extent the company succeeds in optimally adapting the strategy for securing the ability to deliver after EOP to the specific boundary conditions of the product as well as the production. In contrast to series production, the production conditions in the post-series phase are often not optimally adapted to the boundary conditions of post-series production. Due to numerous other challenges in post-series production, such as the availability of operating resources and components, a lack of employee qualification as well as decreasing quantities after the end of production, the conditions are especially aggravated with regard to the costs incurred. On the one hand, rising set-up and commissioning costs per unit are to be expected. On the other hand, production in larger batches increases the length of time the products remain in the warehouse, which results in rising storage and capital commitment costs.
Objective
The aim of the research project is therefore to support the selection of a cost-optimised strategy for post-series production or stockpiling of spare parts after the end of production. The starting point here is the integration of spare parts requirements into the current production in order to be able to use the existing production environment and thus synergy effects.
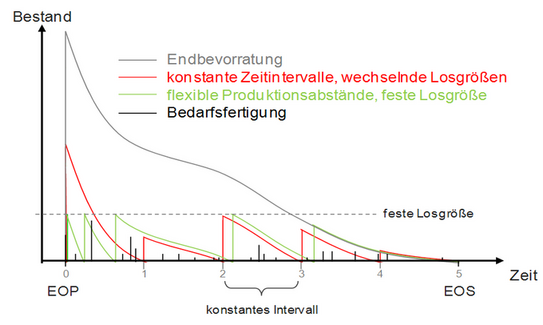
Especially in the case of multi-stage production processes, there is also the possibility of defining different strategies (stockpiling, production in constant (flexible) batches at flexible (fixed) time intervals as well as on-demand production) for individual production stages (value-added steps) in order to minimise the cost effects listed above. Accordingly, a combination of strategies for different production stages is pursued, which can be considered both at the level of finished parts and for different components.
Through such a combination, generally applicable strategies are developed on the basis of which the post-series supply can be controlled. These strategies show at which point in time and in which batch size production orders for post-series production can be harmoniously integrated into the existing production programme of each production stage.
To identify a suitable strategy, a cost model is developed in which the company-specific boundary conditions (e.g. storage cost rates), the product-specific parameters (e.g. set-up costs) and the production and logistics costs induced by them in the production of spare parts are mapped. In this context, the costs of loading spare parts requirements into current production are taken into account in particular. To this end, all factors influencing production and logistics are first determined and quantified by identifying and allocating relevant costs and cost drivers. In addition to the quantitative influencing factors, qualitative factors are also taken into account, which are to be included in the strategy development. The aim is to select an optimal strategy with relatively little input data.
Procedure
The research project comprises six work steps and the continuous documentation of the results over the processing period. In the first step, the post-series production is analysed. This involves analysing and classifying existing post-series supply concepts and general customer requirements on the basis of selected SMEs in expert interviews. The aim is to identify typical and relevant processes for post-series production. Furthermore, production stages or areas are determined which have similar characteristics and are comparable with regard to the requirements of post-series production. Next, general costs (e.g. production stage-dependent costs, storage costs, set-up costs, etc.), cost rates and processes are examined.
This is followed by the definition of the strategies. Based on the processes examined in step one, generally applicable concepts for post-series production are examined and combined into strategies. The strategies are designed in particular with regard to the different production stages.

The cost model is developed on the basis of the previously developed strategies. Since the costs associated with the strategies are particularly decisive for the selection of an optimal strategy, costs and cost drivers are examined for the individual strategies. The aim is to identify cost drivers in such a way that an optimal strategy can be identified with a relatively small amount of data. On the basis of performance measures (cost drivers), the corresponding costs can be assigned to the strategies and thus their impact relationships can be made transparent. In addition, other influencing variables (e.g. flexibility, adherence to schedules, control effort, etc.) are examined, which are relevant in the selection of a strategy and are taken into account in the calculation approach.
After the cost model has been created, the fourth step is to validate the model and thus check whether it represents the real system sufficiently accurately. It is checked whether the determined costs and cost drivers adequately describe the structure and the course of the actual costs. For this purpose, it is necessary to define application scenarios that are used to check the processes in the environment of concrete company data.
Subsequently, general correlations between the boundary conditions of a company and the basic strategies are derived and documented on the basis of the previously developed model and taking into account the interdependencies of cost drivers and strategies. The aim is to be able to identify the optimal strategy for a given initial situation with little effort.
Finally, a data processing tool is developed that enables companies to model their own strategies and boundary conditions and to identify an optimal supply strategy for a specific company.
In order to provide all interested companies with easy access to the project results, the final report will be published on the Internet.
Publications
- Finke, Y.: Schlussbericht: Kostenoptimale Produktions- und Bevorratungsstrategie nach End of Production (EOP), Herausgegeben von Jochen Deuse, Lehrstuhl für Arbeits- und Produktionssysteme, Technische Universität Dortmund. Dortmund, Juni 2010
- Finke, Y.: Kostenoptimale Nachserienproduktion auf Basis von Produktionsstufen, Vortrag auf dem zweiten Kolloquium (Sitzung des projektbegleitenden Ausschusses) zum IGF-Forschungsvorhaben. Dortmund, REFA Business School am 27.01.2010.
- Finke, Y.: Strategien für die verschwendungsarme Nachserienproduktion, Vortrag auf dem ersten Kolloquium (Sitzung des projektbegleitenden Ausschusses) zum IGF-Forschungsvorhaben. Dortmund, Dortmunder Initiative zur rechnerintegrierten Fertigung (RIF) e. V. am 27.04.2009.
Funding Reference
The research project (Research Project No. 15697 N) has been funded from the budget of the Federal Ministry of Economics and Technology via the Federation of Industrial Research Associations "Otto von Guericke" e.V. on behalf of the Federal Logistics Association.