EOP
Kostenoptimale Produktions- und Bevorratungsstrategie nach End of Production (EOP)
Problemstellung
Im Maschinen- und Anlagenbau kommt der Sicherung der Nachserienversorgung sowohl auf Basis ggf. bestehender Nachlieferverpflichtungen als auch in Bezug auf die Kundenbindung eine zentrale Bedeutung zu. Zudem trägt der Verkauf von Ersatzteilen nach dem Auslaufen der umsatzstarken Serienproduktion (End of Production) als ein maßgeblicher Teil des After-Sales-Service zum Unternehmensergebnis bei. Daher ist das hohe Potenzial des After-Sales-Geschäftes zur Steigerung des Unternehmensergebnisses zu nutzen und die Nachserienversorgung entsprechend wirtschaftlich zu gestalten.
Zur Sicherung der Nachserienversorgung werden verschiedene Normstrategien eingesetzt sowie über die Lebenszeit des Ersatzteils zu Versorgungsszenarien kombiniert. Hier besteht die Möglichkeit zur Nachfertigung (intern/extern), zur Nutzung abwärtskompatibler Teile der Serie sowie zur Aufbereitung und Wiederverwendung von Altteilen. Jede dieser Strategien ist durch spezifische Herausforderungen gekennzeichnet, bspw. besteht bei der Altteilwiederverwendung das Problem einer adäquaten Rückführung der Altteile und einer entsprechend großen Rückläuferzahl, um die gegebene Ersatzteilnachfrage zu bedienen.
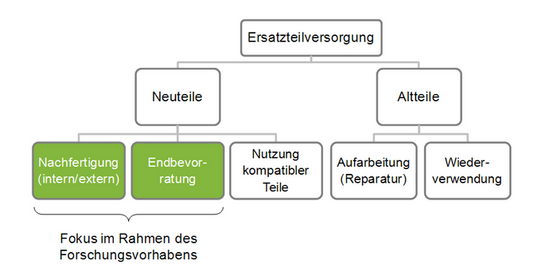
Das hier beschriebene Forschungsvorhaben konzentriert sich auf die Auswahl von Strategien zur Nachserienproduktion und Bevorratung von Ersatzteilen oder deren Komponenten. Für die Nachserienproduktion ist es entscheidend, inwieweit es dem Unternehmen gelingt, die Strategie zur Absicherung der Lieferfähigkeit nach EOP optimal an die spezifischen Randbedingungen des Produktes sowie der Produktion anzupassen. Im Gegensatz zur Serienproduktion sind die Produktionsbedingungen in der Nachserienphase oftmals nicht optimal an die Randbedingungen der Nachserienfertigung angepasst. Durch zahlreiche weitere Herausforderungen in der Nachserienproduktion, wie u. a. die Verfügbarkeit von Betriebsmitteln und Bauteilen, mangelnde Mitarbeiterqualifikation sowie sinkende Stückzahlen nach End of Production, sind speziell in Bezug auf die entstehenden Kosten verschärfte Bedingungen gegeben. Auf der einen Seite sind steigende Rüst- sowie Inbetriebnahmekosten pro Stück zu erwarten. Auf der anderen Seite steigt bei der Produktion in größeren Losen die Verweildauer der Produkte im Lager, wodurch steigende Lager- und Kapitalbindungskosten entstehen.
Zielsetzung
Ziel des Forschungsvorhabens ist folglich die Unterstützung bei der Auswahl einer kostenoptimalen Strategie zur Nachserienproduktion bzw. Bevorratung von Ersatzteilen nach End of Production. Ansatzpunkt bildet hier die Integration von Ersatzteilbedarfen in die laufende Produktion, um die bestehende Produktionsumgebung und damit Synergieeffekte nutzen zu können.
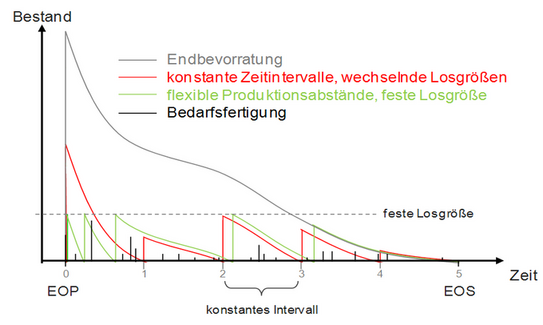
Insbesondere bei mehrstufigen Produktionsprozessen besteht zudem die Möglichkeit, unterschiedliche Strategien (Bevorratung, Fertigung in konstanten (flexiblen) Losen bei flexiblen (festen) Zeitintervallen sowie Bedarfsfertigung) für einzelne Produktionsstufen (Wertschöpfungsschritte) festzulegen, um die oben aufgeführten Kosteneffekte zu minimieren. Dementsprechend wird eine Kombination von Strategien für unterschiedliche Produktionsstufen verfolgt, die sowohl auf Ebene der Fertigteile als auch für unterschiedliche Komponenten betrachtet werden kann.
Durch eine derartige Kombination werden allgemeingültige Strategien entwickelt, auf Basis derer die Nachserienversorgung gesteuert werden kann. Diese Strategien zeigen auf, zu welchem Zeitpunkt und in welcher Losgröße Fertigungsaufträge zur Nachserienproduktion harmonisch ins bestehende Produktionsprogramm jeder Produktionsstufe integriert werden können.
Für die Identifikation einer geeigneten Strategie wird ein Kostenmodell entwickelt, in dem die unternehmensspezifischen Randbedingungen (z. B. Lagerkostensätze), die produktspezifischen Parametern (z. B. Rüstkosten) und die damit induzierten Produktions- und Logistikkosten in der Fertigung von Ersatzteilen abgebildet werden. In diesem Zusammenhang werden speziell die Kosten einer Einlastung von Ersatzteilbedarfen in die laufende Produktion berücksichtigt. Hiezu werden zunächst sämtliche Einflussgrößen auf die Produktion und Logistik ermittelt und quantifiziert, in dem relevante Kosten und Kostentreiber identifiziert und zugeordnet werden. Neben den quantitativen Einflussgrößen werden auch qualitative Größen berücksichtigt, die bei der Strategiefindung einzubeziehen sind. Dabei soll mit relativ wenigen Eingangsdaten eine optimale Strategie ausgewählt werden.
Vorgehensweise
Das Forschungsvorhaben umfasst sechs Arbeitsschritte und die durchgängige Dokumentation der Ergebnisse über den Bearbeitungszeitraum. Im ersten Arbeitsschritt erfolgt die Analyse der Nachserienproduktion. Hierbei werden anhand von ausgewählten KmU in Expertengesprächen bestehende Nachversorgungskonzepte sowie allgemeine Kundenanforderungen analysiert und klassifiziert. Ziel ist es, typische und relevante Prozesse zur Nachserienproduktion zu identifizieren. Des Weiteren werden Produktionsstufen bzw. -bereiche bestimmt, welche hinsichtlich der Anforderungen der Nachserienproduktion ähnliche Eigenschaften aufweisen und vergleichbar sind. Als Nächstes werden allgemeine Kosten (z.B. produktionsstufenabhängige Kosten, Lagerkosten, Rüstkosten, etc.), Kostensätze und verläufe untersucht.
Im Anschluss erfolgt die Definition der Strategien. Ausgehend von den in Arbeitsschritt eins untersuchten Prozessen werden allgemeingültige Konzepte zur Nachserienproduktion untersucht und zu Strategien zusammengefasst. Die Ausgestaltung der Strategien erfolgt insbesondere in Hinblick auf die unterschiedlichen Produktionsstufen.

Auf Basis der zuvor entwickelten Strategien wird das Kostenmodell entwickelt. Da für die Auswahl einer optimalen Strategie insbesondere die mit den Strategien zusammenhängenden Kosten ausschlaggebend sind, werden für die einzelnen Strategien Kosten und Kostentreiber untersucht. Ziel ist es, Kostentreiber in der Weise zu identifizieren, dass mit einer relativ geringen Datenmenge eine optimale Strategie identifiziert werden kann. Anhand von Leistungsmaßgrößen (Kostentreibern) können den Strategien die entsprechenden Kosten zugeordnet und somit ihre Wirkbeziehungen transparent gestaltet werden. Darüber hinaus werden weitere Einflussgrößen (z.B. Flexibilität, Termintreue, Steuerungsaufwand, etc.) untersucht, die bei der Auswahl einer Strategie relevant sind und beim Berechnungsansatz berücksichtigt werden.
Nachdem das Kostenmodell erstellt worden ist, wird im vierten Arbeitsschritt das Modell validiert und folglich überprüft, ob es das reale System hinreichend genau abbildet. Es wird überprüft, ob die ermittelten Kosten und Kostentreiber die Struktur und den Verlauf der tatsächlichen Kosten adäquat beschreiben. Hierzu ist es erforderlich, Anwendungsszenarien zu definieren, anhand derer die Überprüfung der Prozesse im Umfeld von konkreten Unternehmensdaten erfolgt.
Im Anschluss werden auf Basis des zuvor erarbeiteten Modells sowie unter Berücksichtigung der Wirkzusammenhänge von Kostentreibern und Strategien allgemeine Zusammenhänge zwischen den Randbedingungen eines Unternehmens und den Basisstrategien abgeleitet und dokumentiert. Ziel ist es, für eine gegebene Ausgangssituation aufwandsarm erkennen zu können, welche die optimale Strategie ist.
Abschließend wird ein DV-Werkzeug entwickelt, das Unternehmen befähigt, eigene Strategien und Randbedingungen zu modellieren und unternehmensspezifisch eine optimale Versorgungsstrategie zu identifizieren.
Um allen interessierten Unternehmen einen einfachen Zugriff auf die Projektergebnisse zu ermöglichen, wird der Schlussbericht im Internet veröffentlicht.
Veröffentlichungen
- Finke, Y.: Schlussbericht: Kostenoptimale Produktions- und Bevorratungsstrategie nach End of Production (EOP), Herausgegeben von Jochen Deuse, Lehrstuhl für Arbeits- und Produktionssysteme, Technische Universität Dortmund. Dortmund, Juni 2010
- Finke, Y.: Kostenoptimale Nachserienproduktion auf Basis von Produktionsstufen, Vortrag auf dem zweiten Kolloquium (Sitzung des projektbegleitenden Ausschusses) zum IGF-Forschungsvorhaben. Dortmund, REFA Business School am 27.01.2010.
- Finke, Y.: Strategien für die verschwendungsarme Nachserienproduktion, Vortrag auf dem ersten Kolloquium (Sitzung des projektbegleitenden Ausschusses) zum IGF-Forschungsvorhaben. Dortmund, Dortmunder Initiative zur rechnerintegrierten Fertigung (RIF) e. V. am 27.04.2009.
Förderhinweis
Das Forschungsvorhaben (Forschungsvorhaben Nr. 15697 N) ist aus den Haushaltsmitteln des Bundesministeriums für Wirtschaft und Technologie (BMWi) über die Arbeitsgemeinschaft industrieller Forschungsvereinigungen "Otto von Guericke" e.V. (AiF) im Auftrag der Bundesvereinigung Logistik (BVL) e.V. gefördert worden.