INDIVA
Individualised Socio-technical Work Assistance for Production
(Project duration: January 2014 to December 2016)
Problem
Demographic change is leading to a significant change in the age structure in Germany. In the next two decades, the proportion of older people in the working population will increase significantly. In the industrial environment, work systems in the various sectors are designed in such a way that employees must have certain physiological prerequisites in order to be able to perform the job.
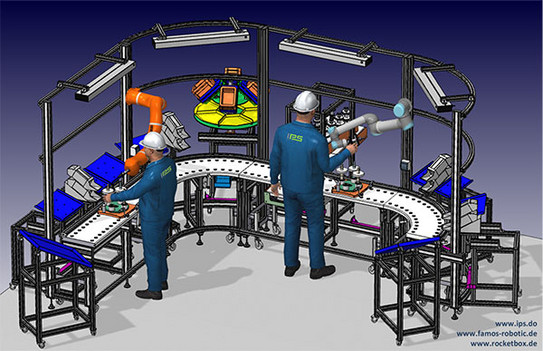
Employees who are limited in age, for example, and can no longer perform the required characteristics to the full extent, then have to change the area of deployment within the company or leave the company prematurely. However, these employees in particular have a wide range of skills and in-depth knowledge due to their often decades of experience. In addition, the ever-increasing shortage of skilled workers and demographic change threaten the availability of labour and thus the effectiveness of German technology leaders of different company sizes. This creates the need to design and adapt work systems for older, experienced employees in such a way that they are individually supported in performing their work according to their abilities.
Objective
The aim of the INDIVA research project is to develop and build a highly flexible, hybrid assembly system with a selective degree of automation and a skill-oriented distribution of tasks between humans and machines.
The focus of the research project is on two sub-areas: On the one hand, an early customisable simulation of the human-machine system is to be used to optimise the coordination of the human-machine interaction under movement-economic, ergonomic and safety aspects, and thus to initially test the assembly system to be developed virtually. On the other hand, a demonstrator of the developed assembly system is to be built and its usability evaluated with future users.
Part of the simulation is a human model that can be individually adapted to different physical ability and performance spectra. This is based on individual movement parameters, such as bending angles and joint positions, recorded by means of a movement recording system, and serves as the basis for the offline programming and simulation of the work assistance system. In this way, individual anthropometric parameters and movement restrictions, if necessary according to the specifications of the company doctor, are to be mapped in the human model to be developed in the future. This individualisation of the human model will make it possible to adjust hybrid assembly systems to the respective abilities of the employee already during planning and to evaluate and adapt them with regard to the physical loads acting on them.
To support the employee in assembly, a robot-supported assistance system is being developed that enables direct collaboration between humans and robots. A central goal is the development of an integrated safety concept to avoid hazards for the employee, which enables direct collaboration between humans and technology. In order to enable the assembly worker to work together with the robot-assisted assistance system and to achieve the desired support, a human-machine interface is being developed for the system that enables safe and intuitive operation as well as flexible coupling of the robot kinematics to the work system. The developed technologies will be implemented in practice by building a demonstrator and verified with its help.
Procedure
The research project pursues the following three directly related, mutually reinforcing and complementary scientific and technical work objectives:
- Development of a procedure for low-effort, computer-aided recording of individual anthropometric (body size) and biomechanical parameters (movement restrictions),
- Development of a software environment for the virtual design of needs-oriented work assistance systems by means of individualisable digital human models,
- Development of a hardware environment for demand-oriented work assistance in industrial assembly to promote healthy and safe work and to ensure entrepreneurial competitiveness.
The expected result is a software and hardware environment that enables companies to identify individual assistance needs through collaborative robotics and to plan and implement appropriate systems. The entire implementation chain, including a demonstrator, will be mapped and implemented with the project. The aim is also to carry out an industry-oriented initial application with the participating partners from industry in car component and pump assembly. This will ensure that the developments can be used in large and medium-sized companies across all sectors.
Research- and Development Partner
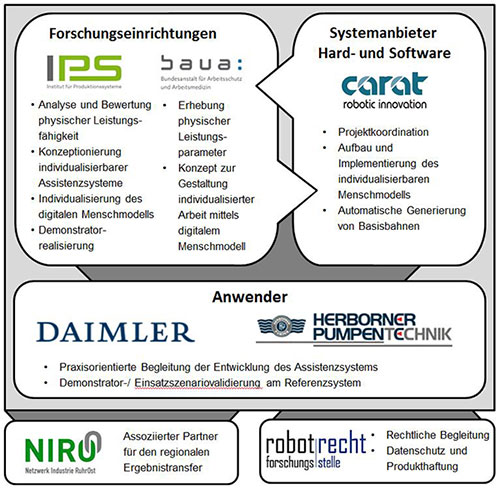
carat robotic innovation GmbH
Federal Institute for Occupational Safety and Health (BAuA)
Daimler AG
Herborner Pumpenfabrik J.H. Hoffmann GmbH & Co. KG
Förderhinweis
This research and development project is funded by the Federal Ministry of Education and Research (FMER) as part of the FMER programme "Technology adapts to people - Innovative interfaces between people and technology" and is supervised by the project management organisation VDIVDE-IT.