Lasercut
Component-independent Fixture for Robot-assisted Laser Cutting
Problem
The cutting of components can be realised by various technical processes. In laser cutting, for example, in addition to the use of conventional laser cutting systems, there is also the possibility of using robot-based solutions with a high degree of flexibility. One of the leading manufacturers of robot-guided laser cutting systems is ROBOT-TECHNOLOGY. This company has developed and markets a laser cutting robot (ROBOCUT) based on an industrial robot by implementing a CO2 laser for cutting plastic, metal and composite components (e.g. for car door panels).
The process of laser-assisted cutting has so far been characterised by the development, design and manufacture of component-specific fixtures. A significant advantage of laser cutting robots compared to conventional laser cutting systems is the high flexibility, but the component provision is currently still severely limited in its flexibility due to the rigid, component-specific fixtures. This has a negative impact on the entire process and brings with it economic as well as financial disadvantages. Due to the necessary change of rigid component fixtures and the resulting set-up times, it is also necessary to keep the fixtures in stock for a repeated production start-up when they are not in use. Due to the necessary lead time for the development and production of new component fixtures, the introduction of new products can only take place with a time delay.
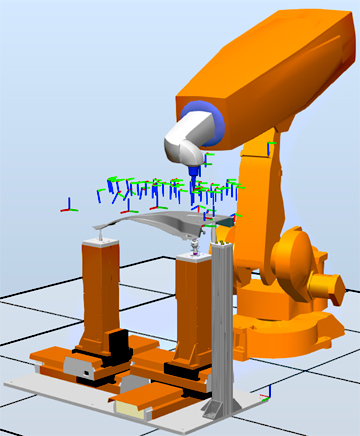
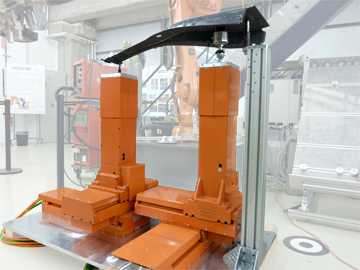
Zielsetzung
Objective
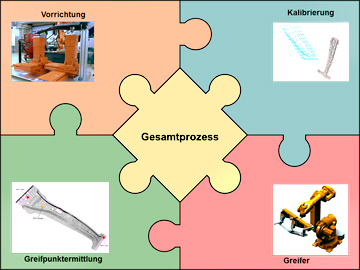
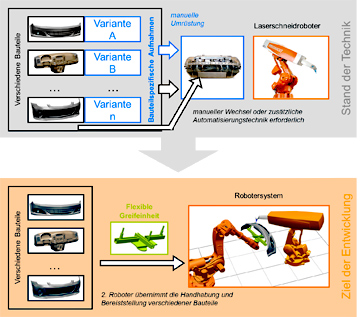
Procedure
The targeted research results were developed in five project phases:
Formulation of requirements and analysis of the component spectrum:
At the beginning of the project, the requirements for the flexible gripping system to be developed were compiled in a specification sheet. In particular, the process characteristics of laser cutting had to be taken into account. The heat input, the processing direction, free cutting contours as well as an unhindered cutting movement were decisive criteria.
Analysis of the contact between component and fixture:
For the design of a flexible clamping and gripping solution, the establishment of contact between the component and the clamping element is of elementary importance. The contact point is used primarily for the transmission of force to the cutting components. The automatic switching on and off of the contact-making process as well as a secure and defined hold of the component, even for three-dimensionally shaped geometries, had to be taken into account. In addition, the type of contact production has an influence on the achievable process accuracy and the reproducibility of the position. Possible physical effects for the implementation include adhesion, cohesion, negative pressure, gravitation, magnetic forces and friction.
Design of a flexible gripping and clamping system:
After defining all process boundary conditions, a static flexible component gripping system was implemented. The concept developed consists of a combination of two electrically driven three-axis linear units and a static support. The two NC linear units allow the contact points to be adapted to the component-specific dimensions. This developed fixture is to replace the previous rigid supports, which are designed and manufactured for each product in a time-consuming and expensive process. This fixture can be directly integrated into the robot control of the laser cutting robot. The units can be fully pre-configured and set up via the manual control unit as well as via the simulation software. This made it possible to set up a flexible fixture with little development effort, which makes it possible to dispense with the component-specific uneconomical fixtures for component families. After the successful implementation of the flexible clamping device, the contact principle, which consists of two mandrels and a vacuum suction cup, was also to be transferred to a flexible gripper.
Configuration of the clamping system on the hand-held control unit:
For the configuration of the gripping system and the control of the moving axes, an integration and control by the robot control IRC5 from ABB was implemented. The laser cutting robots of the project partner ROBOT-TECHNOLOGY are operated with such a robot controller and together with the additional handling robot and the gripping system, the device was integrated into a multi-robot system.
Component calibration:
Since clamping and gripping of the various components always involves certain positioning inaccuracies, the parts must be calibrated before machining. In this way, previously programmed machining paths can be adapted to the current conditions. For the LaserCut project, two different variants were implemented during the project runtime. On the one hand, a component calibration was carried out over three levels, as is usual in coordinate metrology, and on the other hand, an elaborate matching algorithm was implemented, which compares a recorded measurement point cloud with the CAD data and then transforms the machining paths.
Research- and Development Partner
ROBOT-TECHNOLOGY GmbH, Kleinhostheim
Funding Reference
The ZIM project Lasercut is funded by the German Federal Ministry of Economics and Technology via the AiF as part of the Central Innovation Programme for SMEs on the basis of a resolution of the German Bundestag.