NiVaK
Development of a Systematic Approach to Production Levelling of Variant-Rich Small-Batch Production (NiVaK)
Problem
Producing companies are currently confronted with the challenge of satisfying individual customer demands and at the same time realising optimal capacity utilisation. In the course of globalisation and the change from seller's to buyer's markets, a new basic trend in customer demand can be observed. Individual solutions are demanded at mass production prices, which significantly increases the number of product variants to be manufactured, but sales and production quantities per product variant show a declining trend.
In order to still be able to guarantee the shortest possible delivery time on the market, companies are forced to accept either large end-product inventories or considerable downtimes of the plants due to increased changeover processes between the variants. In order to be able to guarantee the shortest possible delivery times and also economical production despite the increasing number of variants, production levelling (Japanese: Heijunka) has proven itself as a production planning method in the context of lean production. The aim of production levelling is to achieve a balanced and harmonised production mix and volume. For this purpose, each product or product variant is produced within a fixed interval. The resulting production cycle is reflected in the so-called EPEI value (Every Part Every Interval).
Objective
The aim of the research project is to develop a systematic approach to production levelling in small batch production with a large number of variants, where the framework conditions for implementing conventional levelling concepts are generally not given. Due to the high number of variants in small batch production, it is first necessary to form a manageable number of product families (so-called levelling families) from the numerous product variants, which can be manufactured together due to their similarity. The formation of levelling families is based on knowledge and methods from group technology.
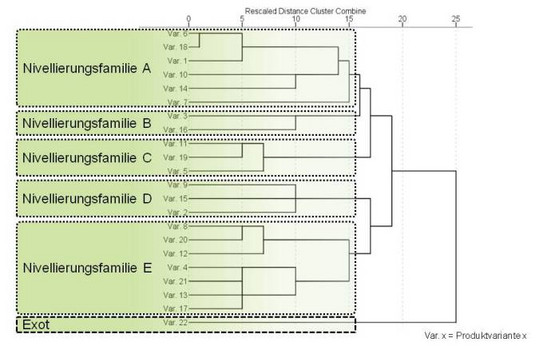
Subsequently, levelling is carried out on a family basis, i.e. time windows are defined in which the individual levelling families are produced. Instead of setting up an EPEI in the sense of producing every product in every interval, the EFEI (Every Family Every Interval) concept is thus being developed within the framework of the research project for the variant-rich small series. Here, the product variants of a levelling family that are currently in demand due to a customer order are produced. The sequence of the time windows and the processing sequence of the orders within a levelling family are determined in a way that optimises set-up time.
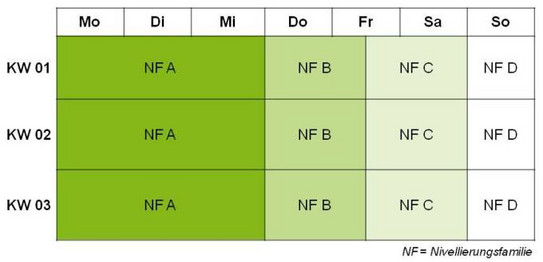
Procedure
The research objective is developed step by step in the form of a total of six work steps. In the first step, relevant product-, process-, labour- and resource-related influencing variables for the formation of levelling families are identified. In the second step, the identified influencing variables are combined into a mathematical evaluation function that enables an automatic comparison of grouping alternatives.
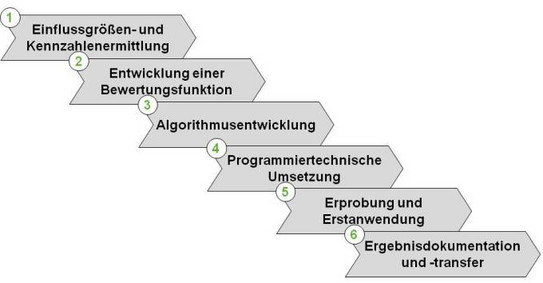
Subsequently, building on the first two steps, an algorithm is developed that formally maps the systematic procedure for production levelling in small batch production with a large number of variants developed within the framework of the project. The algorithm enables both the formation of the levelling families and the generation of the levelling pattern, i.e. the determination of the processing sequence of the families or the orders within the families.
In the fourth step, the developed algorithm is implemented in the form of a data processing tool. In the fifth step, the algorithm is tested in practice and applied for the first time. The systematic procedure, the algorithm and the data processing tool are examined with regard to their applicability in operational practice. In the last step, the collected research results are documented in a comprehensive final report. For documentation and transfer purposes, an internet-based information platform will also be set up. This offers interested companies the opportunity to use the research results.
Publications
Deuse, J.; Birkmann, S.; Harms, T.: Einsatz der Gruppentechnologie zur Nivellierung in der variantenreichen Kleinserie, Industrie Management 23 (2007) 6, S. 45-48.
Funding Reference
The research project (research project no. 15865 N) is funded from the budget of the Federal Ministry of Economics and Technology via the Federation of Industrial Research Associations "Otto von Guericke" e.V. on behalf of the Association for Transport Economics and Logistics (Gesellschaft für Verkehrsbetriebswirtschaft und Logistik e.V.).