Powergrind
Development of a Holistic Concept for Increasing the Material Removal Rate of Robot-Assisted Belt Grinding Processes with Special Consideration of the Influence of Novel Contact Wheels
Problem
In recent years, the demands on the quality of surfaces have constantly increased. Both in the field of design surfaces (e.g. sanitary fittings) and in the field of functional surfaces (e.g. turbine blades), surface qualities are often required that cannot be achieved without additional fine machining. In addition to the trend towards ever-increasing demands on the quality of surfaces, there is also a trend towards increasingly complex, free-formed surfaces. Along with the constant demand for ever more efficient production processes, this results in a multitude of sometimes contradictory requirements for the machining process used.
One process that has established itself in this area of tension in recent years is belt grinding with an elastically deformable contact wheel. On the one hand, it is particularly suitable for the fine machining of free-form surfaces, as the elastic contact wheel enables two-dimensional machining due to its adaptability to the workpiece surface. On the other hand, belt grinding with an elastic contact wheel stands out from other fine machining processes due to its higher stock removal rate with the same or even better surface quality.
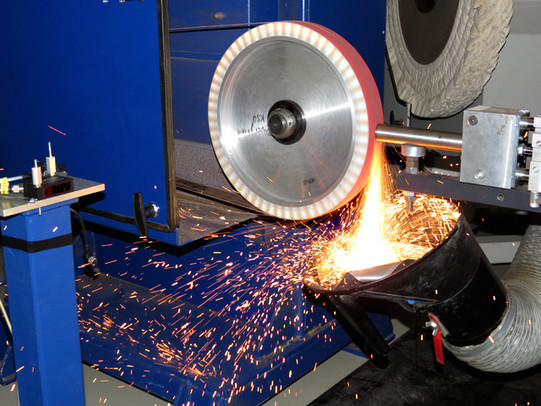
Objective
The aim of the project applied for here is to fundamentally further develop an essential component of the tool, the contact wheel, with the aim of significantly increasing the removal rate in robot-assisted belt grinding and thus improving the economic efficiency of belt grinding processes. The resulting increase in productivity will significantly increase the competitiveness of industries that use belt grinding processes as part of their manufacturing and production chain, such as the sanitary fittings industry or toolmaking.
Procedure
The targeted research results will be developed in stages in the form of 16 work packages (WP).
Research- and Development Partner
The Remscheid-based family business Friedrich August Picard GmbH & Co. KG has been one of the leading manufacturers of grinding, polishing, brushing and deburring tools as well as contact wheels for belt grinding in the metal and woodworking industry for more than 100 years. The products, which are often patented and therefore unique on the market, are mostly the result of Picard's existing cooperations in the grinding and polishing industry.
In addition to its own products, Picard also offers its customers coated abrasives (abrasive belts), robot-controlled grinding and polishing centres, grinding machines, polishing machines, hand-guided machines, extraction systems and much more. Picard's claim is to convince its customers of its products through intensive consultation and testing and thus to realise high-quality and cost-effective high-performance processes in their companies together with them. As a system provider in the field of grinding and polishing, Picard offers everything from a single source - always based on an optimal machining process - from the machine to a robot to the extraction system.
Funding Reference
The ZIM project Powergrind is funded by the Federal Ministry of Economics and Technology via the AiF as part of the programme "Central Innovation Programme for SMEs" on the basis of a resolution of the German Bundestag.