ReProDiPro
Standardisation of the Reference Planning Process of Digital Product Creation (ReProDiPro)
Problem
While mature software systems (CAx, PLM, MES, ERP, PPS, etc.) are used universally in the design and production areas, isolated solutions are usually still found in the intermediate task area of production planning. The tools used here were often procured on the basis of current needs - using the so-called "cherry-picking" method - and then used individually and in isolation for tool-specific planning tasks. Analogous to the IT landscape, the applied planning processes therefore also show a picture that is not coordinated, often even department-centred.
The result is that the individual planning tasks often do not run in a clearly structured way. This leads to inefficient planning processes with redundant procedures, duplication of work, transmission errors and incomplete information, to mention just a few obstacles. Therefore, a standardisation of the necessary planning processes based on best-practice experience in the area of action of production planning can raise many untapped potentials. This then serves the user as an instruction manual for his various planning tasks, whereby the individual processes can run in a simplified and transparent manner.
Objective
The aim of the joint project is the further development and standardisation of a reference planning process for digital product creation. In a first step, this is to be manifested as a DIN draft and then lead to an international ISO standard. This standardisation is intended to achieve a higher level of commitment for manufacturing companies.
With the help of the reference planning process of digital product creation, relevant planning steps and activities of the product creation process are to be systematically described according to defined rules and standardised methods independent of the company. Each planning stage explains which planning methods can be used. In addition, the reference planning process describes in the form of best practices how support can be provided by digital tools.
Procedure
General and company-specific organisational aspects are taken into account when defining the reference process. As a result, the reference process is not limited to digital alone, but also takes into account established methods that have so far only received insufficient computer support. Such a generally valid reference process for product creation forms the basis for company-specific planning processes.
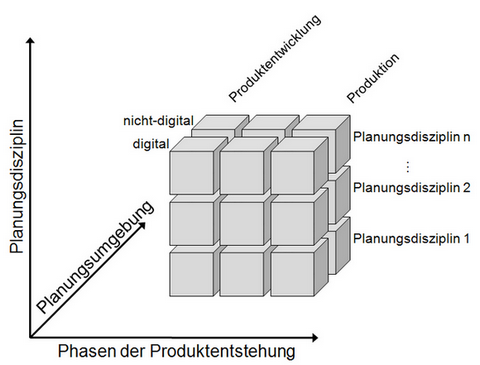
The reference planning process helps both producing companies and developers of planning tools. Producing companies, i.e. the users of planning methods, receive essential assistance when it comes to improving their own planning process. Software developers and service providers can use the reference planning process in the development of new methods and tools, which are then much better tailored to the process chain. For example, providers of complete solutions for the digital factory or PLM systems in general can align their planning tools with a defined planning process so that the tools offer greater consistency and support for the companies' planning process chain. SMEs in particular, which cannot fully exploit the potentials shown above, benefit from such standardisation.
Funding Reference
The project is funded within the framework of the funding programme "Transfer of R&D results through standardisation" by the Federal Ministry of Economics and Technology on the basis of a resolution of the German Parliament (funding code 01FS10050) and is supervised by the project management organisation Work Design and Services at the German Aerospace Centre.