Roprof
Robot Welding of Individually Designed Steel Construction Profiles in Smallest Quantities
Problem
Modern public and industrial buildings such as halls or sports stadiums are largely realised by small and medium-sized steel construction companies. Here, too, automation has long been used in production to improve quality and efficiency and to secure the existence of the company. This has not yet been the case in the important area of welding attachments to steel beams. Although a significant part of the value creation takes place here, the variety of different components in very small quantities has so far made economic automation impossible. In contrast, there is a strong need for automation and a high demand potential for suitable welding robot systems that are designed to meet the special requirements of steel construction. Therefore, within the scope of this project, a welding robot system is to be realised that enables the automated welding of profile components in very small quantities. In order for the systems to be economically integrated into production, they must be flexible, the process times must be short, the reliability and production quality must be high and the operation must be very simple. Products currently available on the market do not meet these requirements.
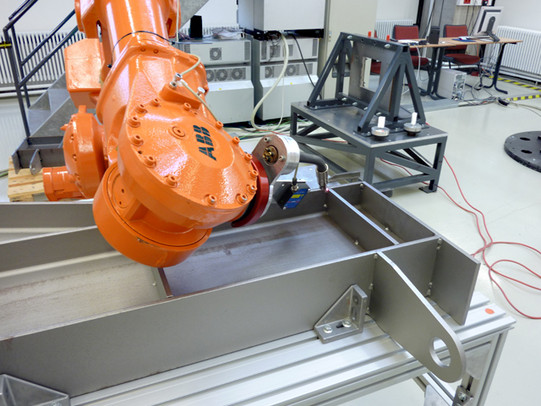
Objective
The key components of the development are a new mechanical design of the robot system that exactly meets the requirements of steel construction companies, automatic robot programming for "learning" new welding tasks in a matter of seconds, and sensor technology that reliably enables the robot to recognise and compensate for the large component pitch inaccuracies that are common in steel construction. The desired technical functionality and parameters are as follows:
A wide variety of attachments are to be welded to hot-rolled or welded steel beams.
The assemblies are usually characterised by a high degree of variation in shape, size, number and position of the attachments.
Small quantities up to batch size 1 have to be produced.
The systems must be suitable for high throughput and multi-shift operation.
The tolerances in steel construction are so large that dimensional deviations have to be compensated for in an automated welding process.
The size of the assemblies usually exceeds the working space of industrial robots without additional axes.
The assemblies must be able to be rotated into different positions to ensure accessibility of the welding positions and a process-appropriate seam position.
It must be possible to operate the equipment by trained welders and also by personnel with low qualifications.
The programming of the system for a new component must be able to be carried out by this personnel within a few minutes.
In order to ensure quick and easy programming of the system, it must be possible to automatically process CAD design data of the components.
Procedure
Field of application in production:
Typical assemblies of steel construction consisting of profiles and add-on parts can be welded in the system. The tacking of the components is done manually, the welding out is done by the robot system. With this division, the most time-consuming work step can be automated, while the scope and risks of the development remain manageable.
Plant layout:
The plant layout is tailored to the specific requirements of steel construction. The variable size of the assemblies requires a robot system with additional axes that can cover a large working area. A suitable component positioner must be developed for welding out the beams in order to make the welding positions accessible to the robot system and to ensure a workpiece position that is favourable for the welding process.
Programming:
The system is programmed fully automatically on the basis of data from a CAD/CAM interface. There are currently no interfaces available on the market that can transfer both the 3D geometry of the assembly and the required welding seam information. To overcome this problem, a concept for a suitable interface has already been developed by the applicant Autocam with the involvement of leading CAD manufacturers in steel construction (bocad Software GmbH, Germany; Construsoft BV, Netherlands - application development for Tekla Corporation, Finland) and the German Steel Construction Association. The focus is on market acceptance and the possibility of a quick introduction. Therefore, the established NC standard of the German Steel Construction Association is to be used for the transfer of the geometry of the assembly components. The assembly information of the subassembly as well as weld seam positions and seam dimensions are transferred by an additional XML document. The planning of all welding, transfer and measuring movements of the robot takes place fully automatically on the basis of the interface data. The system operator can influence both the welding parameters and the process sequence - welding sequence, direction, etc. - if required.
Manufacturing:
The automatically generated machining programmes can be executed directly on the robot controller. The welding seam positions determined on the basis of the CAD model are corrected by measuring the component. The measuring movements, the control of the sensors and the calculation of the corrected path positions are part of the scope of the machining programmes.
Research- and Development Partner
Autocam Information Technology GmbH
Kaltenbach GmbH + Co. KG
Förderhinweis
The ZIM project RoProf is funded by the Federal Ministry of Economics and Technology via the AiF as part of the programme "Central Innovation Programme for SMEs" on the basis of a resolution of the German Bundestag.