rorarob
Welding Task Assistance for Pipe and Frame Constructions by a Robot System
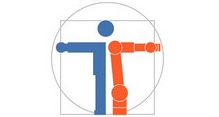
Problem
The welding of pipe and frame constructions is of great importance in the medium-sized machine and plant construction industry. Due to the small quantities up to single-part production, this area represents a labour-intensive production process which is predominantly characterised by manual workplaces and a low degree of mechanisation and automation. The often bulky and heavy components make handling difficult and lead to unfavourable forms of static holding and posture work, especially in joining processes such as welding, and the associated positioning processes, and thus to a hardly avoidable high physical strain on the employee. Furthermore, the production of pipe and frame connections can often only take place after completion of the core systems due to necessary adaptation work and individual connection dimensions, which results in long throughput times.
Objective
In the three-year research project "rorarob - welding task assistance for pipe and frame constructions by a robot system", an industrially applicable system is to be developed in which the interaction between humans and robots is central. This places particularly high demands on the guarantee of occupational safety and compliance with strict legal regulations. In the project, new technologies and concepts in the areas of work planning, ergonomic workplace design, collaborative robot systems, process safety and human-robot interaction are to be developed and implemented in a demonstrator.
With the flexible use of a robot as a mechatronic, (partially) autonomously working assistant using the example of a welding process, the project makes a significant contribution to increasing the acceptance of automated manufacturing systems. Among other things, such a system contributes to
- increase the flexibility of socio-technical systems
- shorten throughput times
- improve ergonomic conditions
- and ultimately to increase economic efficiency and competitiveness.
With the help of this robot-based assistance system, it should be possible to carry out the tube and frame production process largely independently of other work steps in the assembly of an entire plant. This makes simultaneous production with other machine and plant components possible, which reduces the overall throughput time of the production process. For example, in future the welding work on the piping of a turbine could be carried out in parallel with the assembly of the core machine. In addition, the assistance system should enable a significant reduction in the physical strain on the employee when carrying out the welding processes. The design of the interaction between humans and the robot system under work-appropriate, safety-related and economic aspects is thus an essential goal of the joint project.
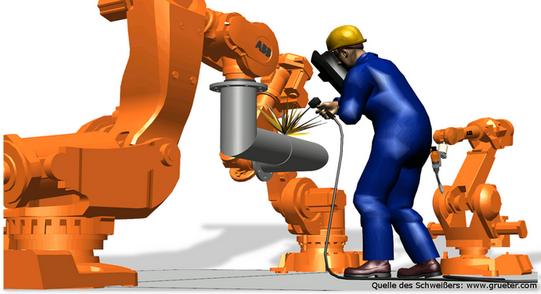
Procedure
The consortium of the rorarob research project, consisting of the Chair of Work and Production Systems (WPS), the Chair of Industrial Robotics and Production Automation (IRPA), a robot system provider and two users in mechanical and plant engineering, intends to develop a multi-robot system for welding task assistance in pipe and frame production within three years, in order to enable employees in production to realise the design specifications in parallel to other production steps, precisely and ergonomically optimised.
The three-year research project rorarob is divided into a total of four project phases:
Phase 1: Analysis and structuring of the requirements for a robot assistance system
Phase 2: Development of concepts for hardware and software implementation
Phase 3: Construction of a robot assistance system (demonstrator) at TU Dortmund University
Phase 4: Validation and optimisation of the project goals on the demonstrator
In the research project, the Chair of Work and Production Systems (WPS) will particularly investigate the aspects of physiological and safety-related work design in a robot assistance system. Physiological work design deals with the forces and stresses acting on the human body during the performance of work. The assistance system to be developed will minimise these types of stress on the employee at the workplace. Furthermore, detailed statements about the extent of the realised improvements can be made within the framework of the project, for example through ergonomic models.
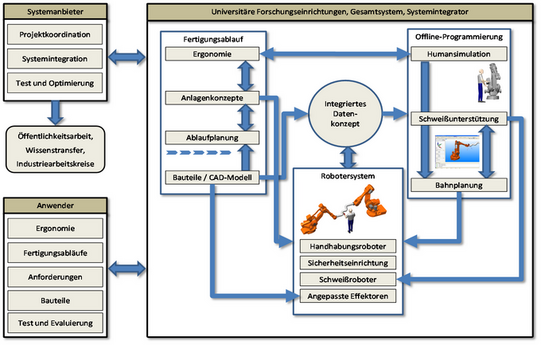
Project video
Robot-assisted Welding Task Assistance for Tube & Frame Constructions
>>> To the rorarob project film: http://www.autonomik.de/de/1075.php
Guides to the AUTONOMIK Technology Programme
- Volume 1: Autonomics - Autonomous and Simulation-based Systems for SMEs
- Volume 2: Law and Functional Safety in Autonomics
- Volume 3: Human-Technology Interaction
- Volume 4: Industrial Service Robotics
- Volume 5: Multimodal Sensor Technology - Concepts of Environmental
- Volume 6: New solutions for Automotive Logistics
Research- and Development Partner
- Chair of Industrial Robotics and Production Automation (IRPA), Faculty of Mechanical Engineering, Dortmund University of Technology
- carat robotic innovation GmbH
- MAN Turbo & Diesel SE
- Böcker Machinery GmbH
Publications
Konferenzen
- Busch, F.; Wischniewski, S.; Deuse, J.: Application of a character animation SDK to design ergonomic human-robot-collaboration. In: Proceedings of the 2nd International Symposium on Digital Human Modeling (DHM2013), Ann Arbor, Michigan (USA), 11.-13.06.2013, PaperID_99
- Busch, F.; Thomas, C.; Deuse, J.; Kuhlenkötter, B.: Development of a Hybrid Robot Assistance System for Welding of Assemblies. Posterpräsentation, Robotik 2012, 21.-22. Mai 2012, München
- Busch, F.; Thomas, C.; Deuse, J.; Kuhlenkötter, B.: A Hybrid Human-Robot Assistance System for Welding Operations – Methods to Ensure Process Quality and Forecast Ergonomic Conditions In: Hu, S. Jack (Hrsg.): Technologies and Systems for Assembly Quality, Productivity and Customization - Proceedings of 4th CIRP Conference on Assembly Technologies and Systems (CATS) 2012, 20.-22.05.2012, Ann Arbor, University of Michigan, Michigan, USA, ISBN 978-0-615-64022-8 , S. 151-154
- Thomas, C.; Busch, F.; Kuhlenkoetter, B., Deuse, J.: Process and Human Safety in Human-Robot-Interaction – A Hybrid Assistance System for Welding Applications In: Jeschke, S.; Liu, H.; Schilberg, D. (Hrsg.): Intelligent Robotics and Applications - Proceedings of 4th International Conference on Intelligent Robotics and Applications (ICIRA2011), 06.-09.12.2011, Aachen, Germany, Verlag Springer Berlin/Heidelberg/New York, ISBN 978-3-642-25485-7 , S. 112-121
- Thomas, C.; Busch, F.; Kuhlenkötter, B.; Deuse, J.: Ensuring Human Safety with Offline Simulation and Real-time Workspace Surveillance to Develop a Hybrid Robot Assistance System for Welding of Assemblies In: Enabling Manufacturing Competitiveness and Economic Sustainability - Proceedings of 4th CIRP Conference on Changeable, Agile, Reconfigurable and Virtual Production (CARV2011), 2.-5. Oktober 2011, Montreal, Canada, Verlag Springer Berlin/Heidelberg/New York 2011, ISBN: 978-3-642-23859-8 , S. 465-470
- Thomas, C.; Busch, F.; Kuhlenkötter, B.; Deuse, J.: Gewährleistung der Humansicherheit durch optische Arbeitsraumüberwachung in der Mensch-Roboter-Kollaboration In: VDI-Berichte 2143 - Automation 2011 (28.-29.06.2011) in Baden-Baden, VDI-Verlag, Düsseldorf 2011, S. 259-262
- Busch, F.; Deuse, J.: Ergonomische Bewertung von manuellen Schweißtätigkeiten mittels Automotive Assembly Work Sheet (AAWS) In: Mensch, Technik, Organisation – Vernetzung im Produktentstehungs- und -herstellungsprozess - 57. Kongress der Gesellschaft für Arbeitswissenschaft e. V., 23.-25.3.2011, GfA-Press, Dortmund, S. 585-588.
- Thomas, C.; Kuhlenkötter, B.: Sichere und kollaborierende Mensch-Roboter-Interaktion – Entwicklung eines robotergestützten Assistenzsystems für das Handling im Schweißprozess, Internationales Forum Mechatronik (IFM) 2010, 03.-04.11.2010, Winterthur (Schweiz), ISBN 978-3-033-02655-1
- Thomas, C.; Brüninghaus, J.: Einsatz kooperierender Mehrrobotersysteme in neuen Anwendungsfeldern, Beitrag zum KooperationsForum Automatisierung und Robotertechnik, veranstaltet von MST Aerospace GmbH. 06.10.2010, Köln
- Thomas, C.; Busch, F.; Kuhlenkötter, B.; Deuse, J.: Safe and Ergonomic Collaboration of Humans and Robots for Welding of Assemblies, Proceedings of 3rd CIRP Conference on Assembly Technologies and Systems (CATS) 2010 “Responsive, customer demand driven, adaptive assembly”, 01.-03.06.2010, Trondheim (Norwegen), S. 121 - 125.
Vorträge
- Thomas, C.: Direkte Mensch-Roboter-Kollaboration in einem Mehrrobotersystem zur Schweißassistenz. Fachseminar Sichere Mensch-Maschine-Kooperation an der Universität Erlangen-Nürnberg, Lehrstuhl für Fertigungsautomatisierung und Produktionssystematik (FAPS), 18.04.2012, Erlangen
- Thomas, C. : Social Implications in Manufacturing Industry (IR@MI). Veranstalter: Karlsruhe Insitute of technology (KIT)
Presse
- Busch, F.; Thomas, C.: rorarob - Schweißaufgabenassistenz für Rohr- und Rahmenkonstruktionen durch ein Robotersystem. In: Productivity Management, 4/2012, GITO Verlag, Berlin, 2012
- „Stärken von Mensch und Roboter vereinen“, verlag moderne industrie GmbH – Produktion Nr. 23, August 2012
- Thomas, C.; Kuhlenkötter, B.; Busch, F.; Deuse, J.: Mensch-Roboter-Kooperation - Humansicherheit im robotergestützten Assistenzsystem. In: atp edition 7-8 2011, 53. Jahrgang, Oldenbourg Industrieverlag, ISSN: 2190-4111, S. 54-61.
- „Assistenzroboter erleichtern dem Schweißer die Arbeit“ verlag moderne industrie GmbH – Produktion Nr. 8, Februar 2011
- „Roboter als Assistenzsystem“ Springer Fachmedien Wiesbaden GmbH – ATZonline, Februar 2011
- „Mensch und Roboter im Team“ schlütersche Verlagsgesellschaft mbh & Co. KG – BLECH 1/2011
- „Kollaborierende Roboter-Assistenten“ Konradin Mediengruppe - Automationspraxis Nr. 6, Juni 2010, Seite 7
- „Autonomik - Autonome und simulationsbasierte Systeme für den Mittelstand“ Bundesministerium für Wirtschaft und Technologie, Mai 2010, Seite 27
- rorarob Projektflyer, Januar 2010
- "Mensch und Roboter arbeiten zusammen", unizet 01/10 Nr.414, S. 7, Dortmund
- "Mensch und Roboter arbeiten zusammen" Industrie- und Handelskammer zu Dortmund - Ruhrwirtschaft 12/09, Dezember 2009, Seite 26
- „Roboter für den Mittelstand“ Technologiezentrum Dortmund News, Dezember 2009, Seite 3
- „Projektauftakt: „rorarob“ entwickelt Einsatz von Robotern in industrieller Produktion“ Pressemitteilung carat robotic innovation GmbH, Dortmund, November 2009
Schlussbericht
- Busch, F.; Deuse, J.: rorarob - Schweißaufgabenassistenz für Rohr- und Rahmenkonstruktionen durch ein Robotersystem - Teilvorhaben: Ergonomische, arbeitsorganisatorische und sicherheitstechnische Gestaltung der Fertigungs- und Anlagenkonzepte, Institut für Produktionssysteme (IPS), Technische Universität Dortmund. Dortmund, Juli 2014
Funding Reference
The project is funded by the Federal Ministry of Economics and Technology as part of the technology programme "Autonomics - Autonomous Simulation-Based Systems for SMEs" based on a resolution of the German Bundestag (funding code 01MA09033) and is supervised by the Multimedia Project Management Agency at the German Aerospace Center.