SafeGrip
Modular System Selection for Process-Safe Gripper and Sensor Technologies
Problem
The safe handling of sensitive objects is a complex issue in robotics, which is currently being addressed in the respective applications primarily with individual developments. An example of this can be provided by companies in the chemical industry or in the medical-pharmaceutical sector. These companies often operate very large storage areas in their laboratories, where millions of test samples of lacquers, pigments, chemical reagents or basic materials for drug production are kept in containers of various sizes. In some critical areas of pharmaceutical laboratory operations, many test samples are very old and virtually unreproducible, so that very great importance must be attached here to the safe handling of substances during order picking. This requires a high degree of grip and positioning safety as well as good monitoring of the handling area including knowledge of other objects in the environment. Frequent errors that lead, for example, to damage or destruction of a test sample are gripping forces that are too high or too low, canting of handling objects, incorrect positioning and incorrect multiple assignments during placement or collision with surrounding as well as other handling objects. In other areas, however, the picking tasks are quite similar, but due to the less problematic retrieval of individual substances, the demands on process reliability are much lower.
What is missing is a pre-selection of gripper and sensor components based on economic constraints, which provides process reliability adapted to the application for specific handling requirements. In most cases, the technically best possible solution causes costs that are not justifiable from an economic point of view. Even the "best necessary" solution is currently mostly developed anew from application to application. Furthermore, when looking at the overall developments of such systems, it is noticeable that the share of the development effort for gripper-sensor combinations often far exceeds the hardware costs of the entire system. Solutions to reduce the expenditure can achieve a considerable increase in the economic efficiency of the later system, especially in this area.
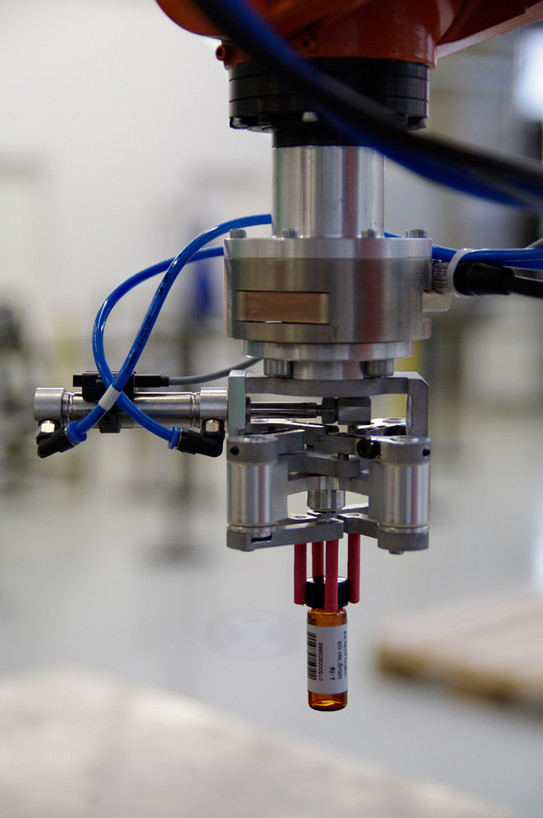
Objective
The SafeGrip project aims to reduce the usually considerable development costs for specific gripper-sensor combinations in order to eliminate the problems described above. For this purpose, a modular system selection for the cost-optimised creation of application-oriented system combinations is to be developed. The development will initially focus on use in pharmaceutical laboratories, although similar applications, such as the storage of pigment and paint samples, will also be taken into account. These should be designed to suit the application and are oriented above all to the alignment with an envisaged plant-related process safety, which can cause considerable costs in the development with increasing requirements. Therefore, the possibility of targeted selection means greater planning security.
The modular system selection should make it possible to configure a cost-effective solution for the predefined process reliability. In the case of the examples of pharmacological test samples mentioned in the problem definition, there is on the one hand the possibility of using a gripper with a higher grip safety or on the other hand to increase the process safety for the existing gripping technology by means of a more complex sensor system (as an example see illustration). By integrating structured drop-out and drop-back strategies into the process, safety is to be additionally improved. The process safety to be achieved with the respective solution will be quantified using a key figure system that is also to be developed.
In SafeGrip, selected application cases are initially considered so that a process safety-related selection system can be set up for this. The methods and solutions developed can be extended for other applications after the project. The gripper-sensor combinations developed can be used directly in related applications, e.g. in the paint or chemical industry, with minor adaptations, while the methodology developed can be transferred to almost all applications that require sensitive, process-safe gripping. In addition, the patenting of self-developed solutions is planned.
Procedure
In the project, grippers and sensor components that can be used as universally as possible are developed or assembled from standard components in accordance with the intended applications. This is followed by the implementation in staged combinations to form a modular system selection. The most important tasks to be carried out for this are listed below:
- Categorisation of gripping operations for different applications.
- Selection and development of handling devices that cover individual categories as far as possible.
- Combination of the handling device with sensor systems
- Investigation of mutual influence of components for optimal use of positive side and synergy effects and avoidance of negative influences
- Development of a key figure system to quantify process reliability as a degree of freedom of the categorised use cases
- Development of failure and relapse strategies
- Testing and validation of category-related process safety
These concern the supporting necessity of defining planning indicators and essential information flows within the reference planning process. The development of a standard basis for an ISO deliverable defined in the objective has the great potential to position a scientifically mature issue developed in the national environment at the international level. The associated international pioneering role enables Germany as a national location to develop a knowledge and market advantage, which represents a clear strengthening in the global competition.
Research- and Development Partner
IBG Automation GmbH
IBG Robotronic GmbH
Funding Reference
This research and development project is funded by the Federal Ministry of Education and Research as part of the BMBF programme "Research for the Production of Tomorrow" and is supervised by the Project Management Agency Karlsruhe.