KoMPI
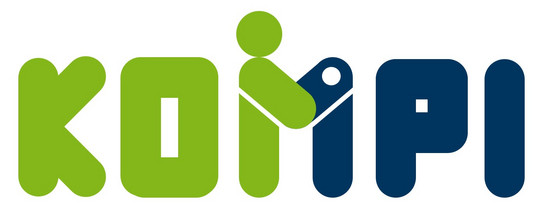
Verrichtungsbasierte, digitale Planung kollaborativer Montagesysteme und Integration in variable Produktionsszenarien (KoMPI)
(Projektlaufzeit: Januar 2017 – Dezember 2019)
Problemstellung
Die Montage industrieller Güter hat in Deutschland einen sehr hohen Wertschöpfungsanteil am Bruttosozialprodukt. Darüber hinaus ist Deutschland im Bereich der Ausrüstung für Montage- und Handhabungstechnik weltweit einer der führenden Anbieter. Aufgrund zunehmend volatiler Märkte, individueller und komplexer Produkte sowie neuer Prozessanforderungen - z. B. durch Industrie 4.0 - ist die Montage besonderen Wandlungsanforderungen ausgesetzt. Wichtig sind deshalb die Entwicklung, Gestaltung und Einführung innovativer Systemlösungen zur Montage komplexer Stückgüter. Dabei stehen die sichere Arbeitsplatzgestaltung und die Kooperation von Mensch und Roboter in der Montage im Fokus. Des Weiteren gewinnt die Wandlungsfähigkeit von Montageanlagen zunehmend an Bedeutung, um auf variierende Stückzahlen reagieren zu können und Investitionsrisiken zu minimieren. So wird es zukünftig möglich sein, mit kollaborativen und wandlungsfähigen Montagelösungen, insbesondere klein- und mittelständischen Unternehmen, Kosten- und Effizienzvorteile zu ermöglichen und die Innovationsführerschaft deutscher Montageanlagenhersteller langfristig zu sichern.
Die Planung eines manuellen Montagearbeitsplatzes, in Bezug auf Arbeitsinhalt und Arbeitszeit, ist eine komplexe Aufgabe. Aufgrund der Vielfalt der dabei zu berücksichtigenden Daten geschieht dies heute meistens mit dafür speziell entwickelter Software zur Modellierung, Simulation und Optimierung der Arbeitstakte der manuellen Montageprozesse. Erwägt ein Unternehmen heute den Einsatz von Arbeitsplatzsystemen, an denen Menschen und Roboter miteinander kollaborieren, gibt es bislang noch keine digitalen Planungswerkzeuge, welche den Einsatz des Systems im Hinblick auf Automatisierbarkeit, technisch-wirtschaftliche Eignung, Ergonomie und Sicherheit simulieren und bewerten können. Dies ist nicht nur für KMU eine starke Hemmschwelle für den Einsatz von kostengünstigen Robotern in Montagesystemen.
Zielsetzung und Vorgehensweise
Ziel des geplanten Forschungsprojektes ist es, eine neue Methode zur integrierten Planung und Realisierung von kollaborativen Arbeitsplatzsystemen in der Montage bei variablen Produktszenarien zu entwickeln. Dies soll sicherstellen, dass auch Unternehmen mit geringer Erfahrung und begrenzten Ressourcen befähigt werden, kollaborative Arbeitssysteme mit Erfolg einzuführen und auch bei stark schwankender Produkt- und Variantenvielfalt dauerhaft wirtschaftlich zu betreiben.
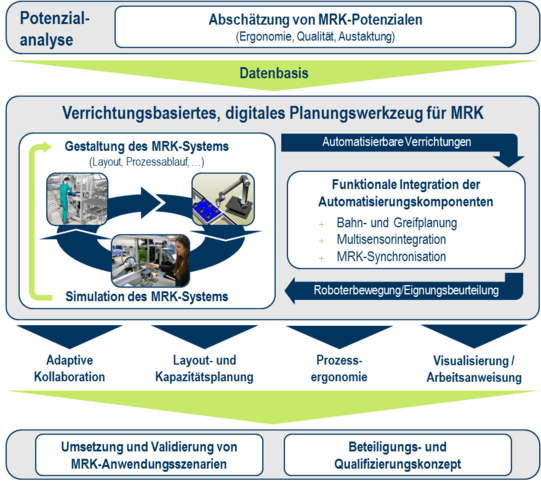
Die Ergebnisse des Verbundprojektes unterstützen den gesamten MRK-Entstehungsprozess: Die neue Methode zur integrierten Planung und Realisierung von kollaborativen Arbeitsplatzsystemen in der Montage soll insbesondere die Arbeitsplaner im Planungs- und Gestaltungsprozess unterstützen. Eine Auswahlsystematik wird zunächst, ausgehend von der Analyse bestehender manueller Montageszenarien, die Arbeitsplätze mit Potential für die Mensch-Roboter-Kollaboration identifizieren. Das Potential wird insbesondere durch die Flexibilität der Roboter begrenzt. Durch die gezielte Verknüpfung optischer Sensorik und Roboter werden die Einsatzbereiche der Robotersysteme erweitert. Die digitale Gestaltung und Bewertung des kollaborativen Arbeitsplatzsystems wird mit einer allgemeingültigen Planungsmethode modelliert. Die Planung wird gemäß der speziellen Montageaufgaben verrichtungsbasiert durchgeführt und durch die zu entwickelnden Roboter- und Komponentenbibliotheken unterstützt, wobei die technische Integration des Roboters und seiner Komponenten simuliert werden kann. Nachfolgend werden die Umsetzung und Integration durch ein technisches Integrationskonzept sowie ein mitarbeiterorientiertes Beteiligungs- und Qualifizierungskonzept gefördert, sodass bestehende technische und soziale Hemmnisse abgebaut werden. Auch während des laufenden Betriebs werden operative Mitarbeiter über zu entwickelnde, geeignete Mensch-Maschine-Schnittstellen gezielt eingebunden und somit die Akzeptanz für den Einsatz von MRK gefördert. Nicht zuletzt wird diese Akzeptanz auch durch die aktive Beteiligung der Sozialpartner gestützt.
Zusammenfassend stehen somit das verrichtungsbasierte Planungssystem in Form einer Software-Lösung für Integratoren und Endanwender mit MRK-anforderungsgerechter Benutzerführung sowie das Beteiligungs- und Qualifizierungskonzept als multimedial aufbereiteter Schulungs- und Trainingsleitfaden zur Seminar- und Workshop-Durchführung bei den Anwendern am Ende des Verbundprojektes KoMPI zur Verfügung. Diese beiden genannten Entwicklungsergebnisse sind anhand der bei und mit den Anwendungspartnern geplanten, umgesetzten und validierten MRK-Applikationen im Projektvorhaben verifiziert worden.
Arbeitsteilung
Das Vorhaben ist auf eine Laufzeit von drei Jahren ausgelegt und gliedert sich in drei Phasen:
In der ersten Phase werden die Anforderungen an das Planungs- und Simulationssystem erfasst. Dabei müssen sowohl technische Restriktionen als auch die unternehmens- und branchenübergreifenden Anforderungen der späteren Anwender berücksichtigt werden. Hierbei erfolgt zudem die Definition der Anwendungsszenarien für unterschiedliche Produktvarianten. Die Anwendungsszenarien sind so gewählt, dass diese unterschiedliche Industriezweige abdecken und die Anwenderunternehmen auch mittelständische Strukturen aufweisen, sodass eine Übertragbarkeit der Forschungsergebnisse auf die deutsche Unternehmenslandschaft sichergestellt ist. Aus der Analysephase ergeben sich wichtige Aspekte für die späteren Schulungs- und Trainingskonzepte der Mitarbeiter im kollaborativen Montagesystem sowie zur Beteiligung der Sozialpartner. Den Abschluss der ersten Phase bildet die Architektur des zu entwickelnden Planungssystems sowie die Spezifikation der Software-Schnittstellen zur Verknüpfung der jeweiligen Systemkomponenten, wie der Roboter- und Peripheriesimulation mit integrierter Komponentenbibliothek, dem Werkzeug zur Potentialabschätzung von MRK-Szenarien und der Logik zur fähigkeitsorientierten Verteilung von Verrichtungen auf Mensch und Roboter.
In der zweiten Phase erfolgen die Entwicklung und Implementierung des Systems sowie die Ausarbeitung der Schulungs- und Trainingskonzepte. Mittels einer auf AutomationML und COLLADA basierenden Schnittstelle soll die Verbindung der einzelnen Teilsysteme und somit die simultane Entwicklung dieser Teilsysteme erfolgen.
Die letzte Phase stellt die Validierung des Gesamtsystems dar. Diese zeichnet sich durch innovative Anwendungsszenarien der kollaborativen Montage in den zuvor beschriebenen unterschiedlichen Branchen aus, die mit Hilfe des entwickelten Systems geplant, ausgestaltet und abschließend in reale Demonstratoren bei den Anwendern umgesetzt werden. Die Erfahrungen aus der digitalen Planung und Simulation der Anwendersysteme werden genutzt, um das Planungssystem zu optimieren und die Konzepte der Schulung und des operativen Trainings zu erproben.
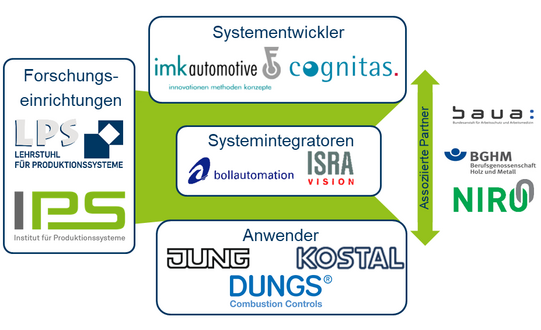
Forschungs- und Entwicklungspartner
- Technische Universität Dortmund, Institut für Produktionssysteme (IPS)
- Ruhr-Universität Bochum, Lehrstuhl für Produktionssysteme (LPS)
- imk automotive GmbH
- ISRA Vision AG
- Boll Automation GmbH
- cognitas Gesellschaft für Technik-Dokumentation mbH
- Albrecht Jung GmbH & Co. KG
- Leopold KOSTAL GmbH & Co. KG
- Karl Dungs GmbH & Co. KG
Förderhinweis
Das Projekt wird im Rahmen des Förderprogramms „Innovationen für die Produktion, Dienstleistung und Arbeit von Morgen“ zum Themenfeld „Kompetenz Montage – kollaborativ und wandlungsfähig (KoMo)“ vom Bundesministerium für Bildung und Forschung (BMBF) gefördert und wird vom Projektträger Karlsruhe (PTKA) betreut.